kullanarak yüksek kaliteli pelet üretimi plastik kırma Çok çeşitli plastik ürünlerin imalatında kritik öneme sahiptir. Ancak yaygın üretim sorunları, düşük kaliteli peletlere, üretimde gecikmelere ve hatta ekipman hasarına yol açabilir.
Bu yazımızda plastik granülatörün üretimi sırasında ortaya çıkabilecek üç yaygın sorunun nedenlerini ve çözümlerini tartışacağız.
Peletlerdeki siyah noktalar
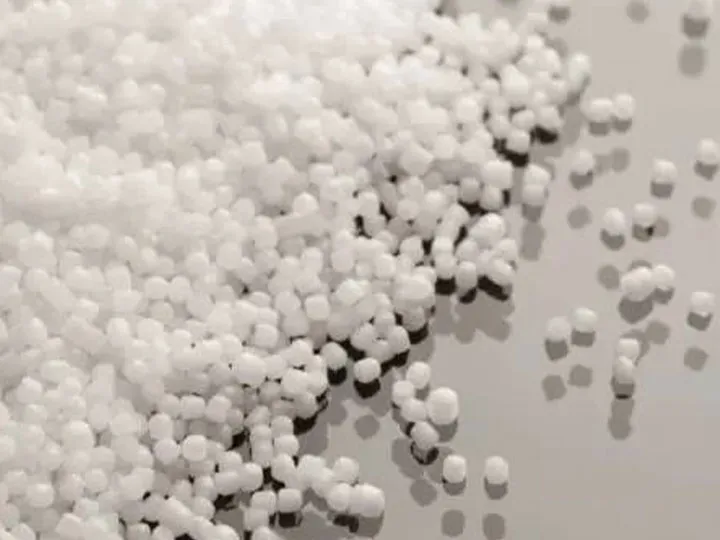
Geri dönüştürülmüş plastik topakların üzerindeki siyah noktalar; malzemenin bozulması, aşırı ısınma ve malzemenin karbonizasyonu gibi çeşitli faktörlerden kaynaklanabilir.
Peletlerdeki siyah nokta problemini çözmenize yardımcı olacak pratik çözümler şunlardır:
- Kaliteli malzemeler kullanın: Kaliteli malzemeler, geri dönüştürülmüş plastik granüllerdeki siyah noktaların önlenmesine yardımcı olabilir.
- Namlu sıcaklığını azaltın: Aşırı ısınma, malzemenin bozulmasına ve siyah noktaların oluşmasına neden olabilir.
- Vida hızını artırın: Vida hızının artırılması, karıştırmanın iyileştirilmesine ve malzemenin karbonizasyonunu önlemeye yardımcı olabilir.
- Hammaddelere ve bitmiş ürünlere yabancı yabancı maddelerin karışmasını önlemek için üretim ortamına ve operasyon sürecine dikkat edin.
Kırık şerit sorunu
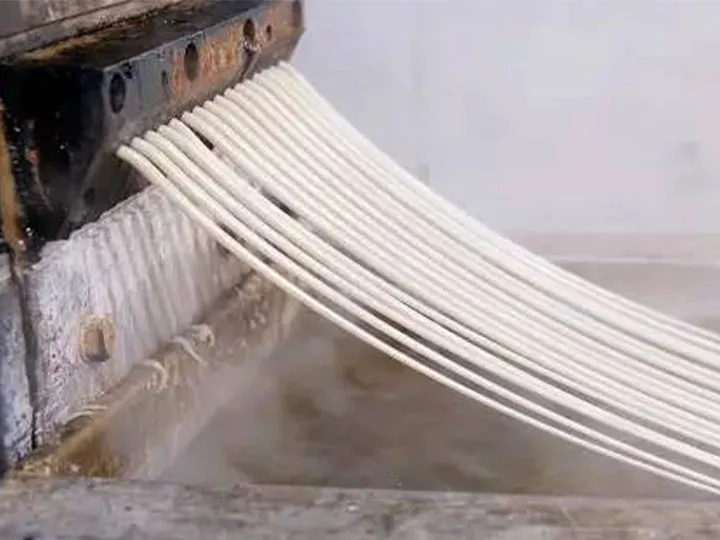
Plastik granülatörde şerit kırılması, peletlerin kalitesini etkileyen yaygın bir sorundur. Şerit kırılmasının yüksek ilerleme hızları, yüksek vida hızları ve aşınmış veya hasar görmüş vidalar gibi çeşitli nedenleri vardır.
Kırık şerit sorununun üstesinden gelmenize yardımcı olacak pratik çözümler şunlardır:
- İlerleme hızını azaltın: Şerit kırılmasının ana nedenlerinden biri aşırı ilerleme hızıdır. İlerleme hızını ekstruderin etkili bir şekilde işleyebileceği bir seviyeye düşürün.
- Çok büyük veya çok sayıda elek ağı, malzeme taşınmasına karşı direnci tetikleyebilir ve şeritlerin kırılmasına neden olabilir. Bu, ana bilgisayar hızını uygun şekilde azaltarak veya besleme hızını artırarak yapılmalıdır.
- Düzenli olarak kontrol edin ve aşınmış veya hasar görmüş vidaları gerektiği gibi değiştirin: Aşınmış veya hasarlı vidalar tutarsız karışıma neden olabilir ve bu da şeritlerin kırılmasına neden olabilir.
- Namlu sıcaklığını artırın: Namlu sıcaklığının arttırılması malzemenin yumuşamasına yardımcı olur ve şerit kırılma riskini azaltır.
- Ekstrüzyon sıcaklığı düşük veya vida kesme kuvveti çok zayıf ve hem malzeme hem de düşük erime noktalı katkı maddeleri yeterince plastikleştirilmemiş; bu da ekstrüzyon peletleme sırasında zayıf plastikleştirilmiş malzemede şerit kırılmasına yol açabilir.
Tutarsız parçacık boyutu
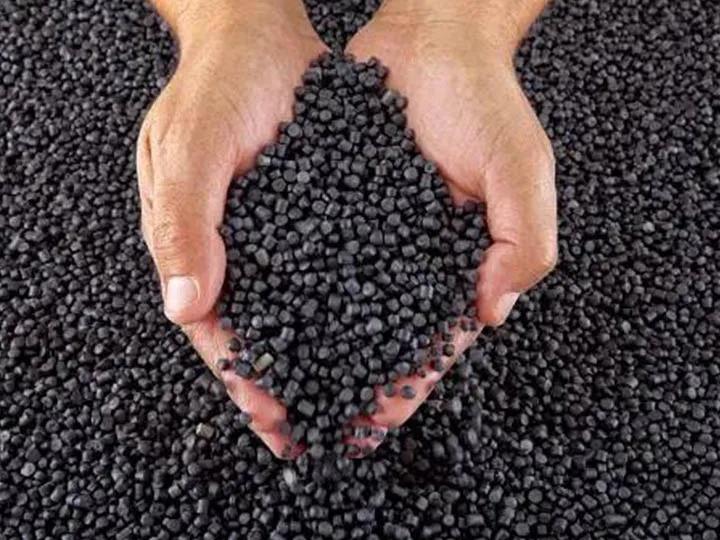
Pelet boyutunda tutarsızlık, plastik granülatörün üretimi sırasında ortaya çıkan bir diğer yaygın sorundur.
Bu soruna tıkalı kalıplar, aşınmış vidalar veya hasarlı kesme bıçakları gibi çeşitli faktörler neden olabilir. Aşağıdaki pratik çözümler bu sorunun üstesinden gelmenize yardımcı olabilir:
- Tıkanmış kalıpları kontrol edin: Tıkalı kalıplar tutarsız parçacık boyutlarına yol açabilir. Tıkanmışsa uygun bir temizleme aletiyle temizleyin.
- Vidaları kontrol edin: Aşınmış vidalar tutarsız tanecik boyutlarına neden olabilir. Aşınmadıklarından veya hasar görmediklerinden emin olmak için vidaları inceleyin. Aşınmışlarsa değiştirmeyi düşünün.
- Kesici bıçakları kontrol edin: Hasarlı kesici bıçaklar tutarsız parçacık boyutlarına neden olabilir. Hasar görmediğinden emin olmak için kesme bıçağını inceleyin. Hasar görmüşlerse değiştirmeyi düşünün.
- Vida hızını ayarlayın: Peletleyicinin vida hızı, boşaltmanın uzunluğunu etkiler ve vida hızının ayarlanması, pelet boyutu tutarsızlıklarının çözülmesine yardımcı olabilir. Tutarlı bir pelet boyutu elde etmek için vida hızını artırabilir veya azaltabilirsiniz.
- İlerleme hızını kontrol edin: Yanlış bir ilerleme hızı tutarsız pelet boyutlarına yol açabilir. Çok yüksek veya çok düşük olmadığından emin olmak için ilerleme hızını kontrol edin. Tutarlı pelet boyutları elde etmek için besleme hızını gerektiği gibi ayarlayın.
Sonuç olarak, plastik granülatörün üretimi, özel duruma göre çözülmesi gereken karmaşık bir süreçtir. Üretim sürecinde, üretim verimliliğini ve pelet kalitesini sağlamak için ekipmanın durumunu kontrol etmeli ve çalışma parametrelerini zamanında ayarlamalısınız.