Con la promoción de la protección del medio ambiente en los últimos años, muchas marcas de consumo han aumentado la proporción de plástico reciclado en sus productos, aumentando considerablemente el uso de filamentos respetuosos con el medio ambiente y, por tanto, la demanda de escamas de botellas de PET de alta calidad. Por lo tanto, es necesario utilizar Línea de lavado de botellas de PET para mejorar la calidad de las escamas de botellas de PET.
Además, la aplicación del reciclaje “botella a botella” de PET y las escamas de calidad alimentaria también ha planteado nuevos desafíos a la calidad de las escamas de botellas de PET recicladas.
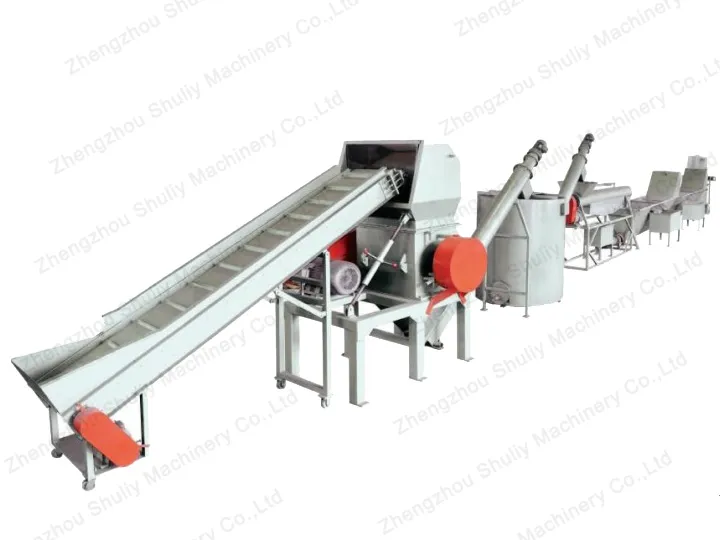
Factores que afectan la calidad de las escamas de las botellas de PET.
Tipo de material plástico
El tipo de material plástico utilizado puede afectar la calidad de las escamas de PET. Por ejemplo, las botellas de PET recicladas suelen producir escamas de mayor calidad que los residuos plásticos mixtos.
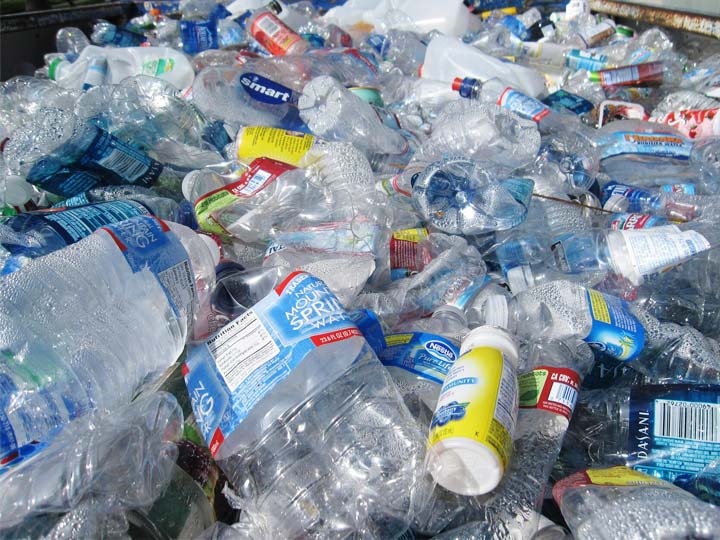
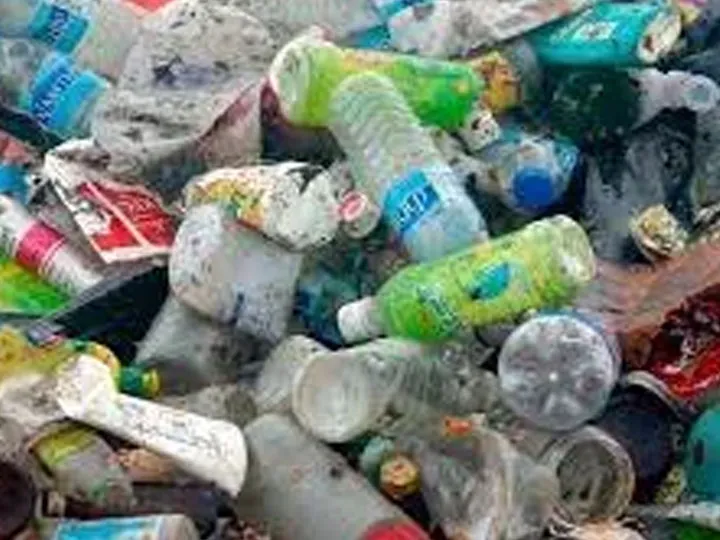
Contaminación
La contaminación puede reducir significativamente la calidad de las escamas de PET. Las fuentes comunes de contaminación incluyen suciedad, aceite y etiquetas. En la línea de lavado de botellas de PET, la eliminación de estos contaminantes es muy importante para la producción de escamas de PET de alta calidad.
Temperatura de procesamiento
La temperatura de procesamiento es otro factor clave que afecta la calidad de las hojuelas de PET. Es importante mantener una temperatura de procesamiento constante para garantizar que el plástico se limpie a fondo y que la calidad del producto final no se vea comprometida.
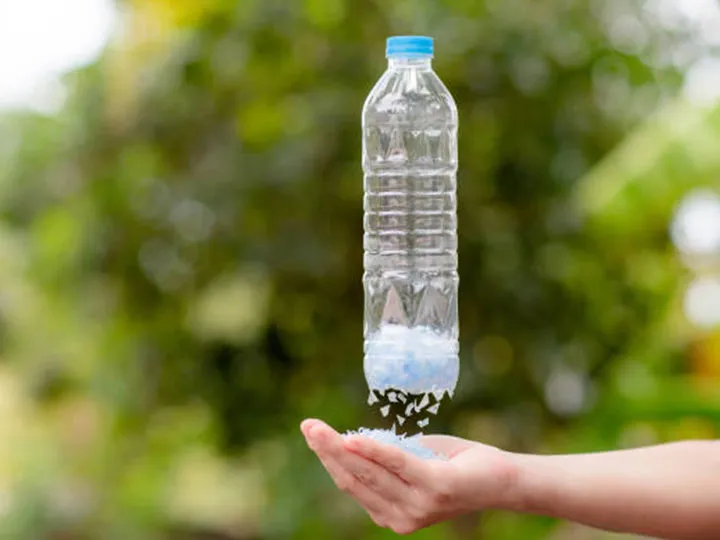
¿Cómo producir escamas de botellas de PET de alta calidad?
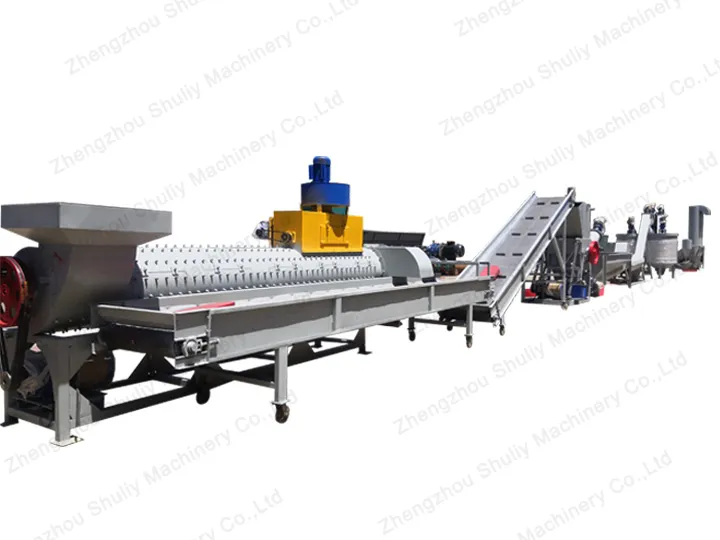
Para utilizar la línea de lavado de botellas de PET para producir escamas de botellas de PET de mayor calidad, le sugiero que pueda:
- Utilice materias primas de alta calidad.
- Optimizar el proceso de lavado.
- Elimina contaminantes e impurezas.
- Utilice equipos de secado de alta calidad.
¿Exactamente cómo debo hacerlo?
Hay varios pasos clave específicos que se pueden tomar para mejorar la calidad de las hojuelas de PET finales en la línea de lavado de botellas de PET. Estos incluyen:
Clasificación correcta de materiales plásticos.
La clasificación adecuada de los materiales plásticos es fundamental para obtener escamas de PET de alta calidad. Esto evitará que contaminantes como etiquetas, adhesivos, papel y otros plásticos que no sean PET entren en la línea de lavado de botellas de PET y contaminen las escamas finales.
Utilice un detergente eficaz
El tipo de detergente utilizado puede tener un impacto significativo en la calidad de las hojuelas de PET finales. A menudo se utilizan reactivos alcalinos fuertes para eliminar la grasa, mientras que los reactivos ácidos son eficaces para eliminar las manchas rebeldes y la decoloración.
Es importante controlar cuidadosamente el pH de la solución limpiadora y ajustarlo según sea necesario para garantizar que el agente limpiador sea eficaz y no dañe el plástico.
Control cuidadoso de la temperatura y el tiempo de lavado:
La temperatura y la duración del proceso de lavado también pueden afectar la calidad de las virutas de PET finales. Las temperaturas más altas pueden aumentar la eficacia del detergente, pero también pueden hacer que el plástico se vuelva quebradizo y se rompa con facilidad.
La temperatura siempre debe mantenerse dentro del rango recomendado para garantizar que el plástico se limpie a fondo y que la calidad del producto final no se vea comprometida.
Mantenimiento y revisión de tendederos.
El mantenimiento y revisión regulares de la línea de lavado de botellas de PET son esenciales para garantizar su funcionamiento óptimo y la producción de escamas de PET de alta calidad.
Esto incluye una línea de lavado de botellas de PET de alta calidad y cualquier equipo auxiliar como trituradora de plastico, transportador y maquina secadora de plastico, comprobando posibles fallos y sustituyendo las piezas desgastadas o dañadas. El equipo debe recibir mantenimiento y actualizarse periódicamente según sea necesario para garantizar un funcionamiento óptimo.
Secado y enfriamiento adecuados
El último paso en la línea de lavado de botellas de PET es secar y enfriar las escamas, que generalmente se calientan para evaporar la humedad restante.
Es importante controlar cuidadosamente la temperatura y la duración del proceso de secado para evitar el sobrecalentamiento y daños al plástico. Los copos enfriados pueden luego recolectarse y almacenarse para su posterior procesamiento o venta.
Si se siguen cuidadosamente estos pasos, se puede mejorar la calidad de las escamas de PET finales en la línea de lavado de botellas de PET. Esto ayuda a maximizar el valor del plástico reciclado y garantiza que sea adecuado para su uso en la producción de nuevos productos PET.
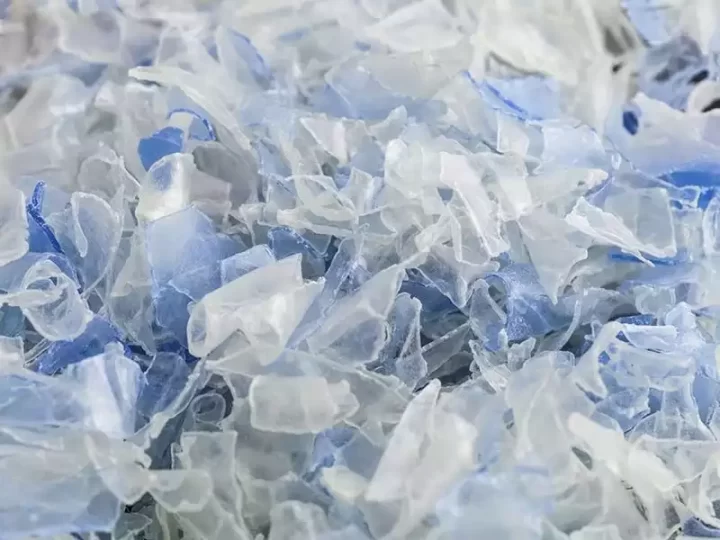
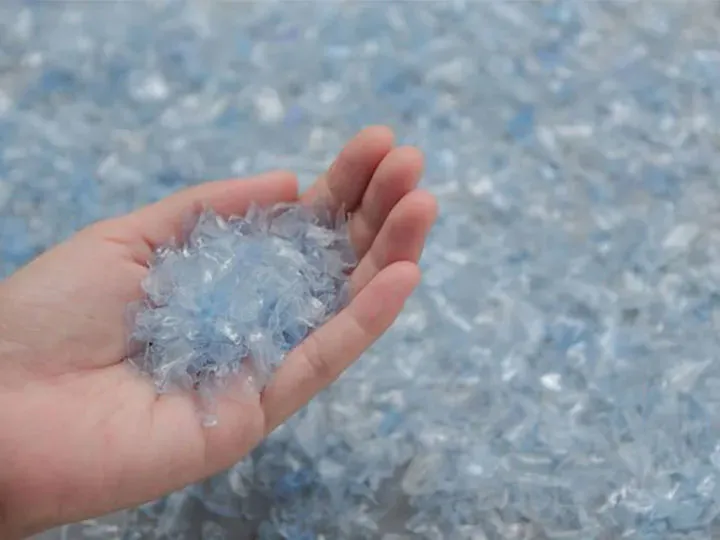