Die Herstellung hochwertiger Pellets erfolgt mit Kunststoffgranulator ist für die Herstellung einer breiten Palette von Kunststoffprodukten von entscheidender Bedeutung. Häufige Produktionsprobleme können jedoch zu Pellets von geringer Qualität, Produktionsverzögerungen und sogar zu Geräteschäden führen.
In diesem Artikel besprechen wir die Ursachen und Lösungen für drei häufige Probleme, die bei der Produktion von Kunststoffgranulatoren auftreten können.
Schwarze Flecken auf Pellets
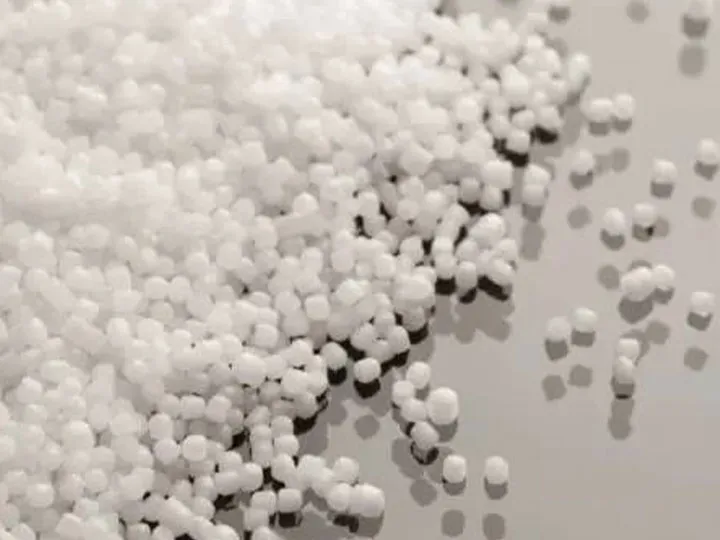
Schwarze Flecken auf recycelten Kunststoffpellets können durch eine Vielzahl von Faktoren verursacht werden, darunter Materialabbau, Überhitzung und Materialkarbonisierung.
Die folgenden praktischen Lösungen helfen Ihnen, das Problem der schwarzen Flecken auf Pellets zu lösen:
- Verwenden Sie hochwertige Materialien: Hochwertige Materialien können dazu beitragen, schwarze Flecken auf recyceltem Kunststoffgranulat zu vermeiden.
- Fasstemperatur reduzieren: Überhitzung kann zu Materialverschlechterung und zur Bildung schwarzer Flecken führen.
- Schneckengeschwindigkeit erhöhen: Eine Erhöhung der Schneckengeschwindigkeit kann dazu beitragen, das Mischen zu verbessern und die Karbonisierung des Materials zu verhindern.
- Achten Sie auf die Produktionsumgebung und den Betriebsprozess, um zu vermeiden, dass Fremdverunreinigungen in die Rohstoffe und Fertigprodukte eingemischt werden.
Problem mit gebrochenem Streifen
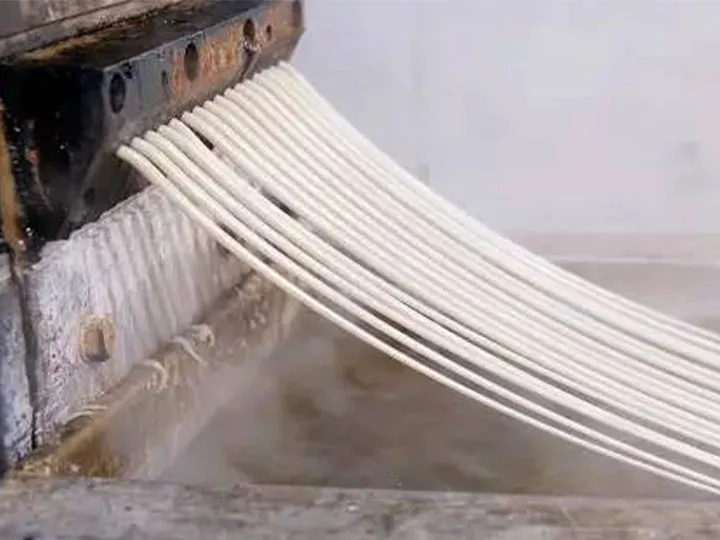
Streifenbrüche in Kunststoffgranulatoren sind ein häufiges Problem, das die Qualität der Pellets beeinträchtigt. Es gibt verschiedene Gründe für Bandbrüche, wie z. B. hohe Vorschübe, hohe Schneckengeschwindigkeiten und verschlissene oder beschädigte Schnecken.
Im Folgenden finden Sie praktische Lösungen, die Ihnen helfen, das Problem gebrochener Streifen zu überwinden:
- Reduzieren Sie die Vorschubgeschwindigkeit: Eine der Hauptursachen für Bandbrüche ist eine zu hohe Vorschubgeschwindigkeit. Reduzieren Sie die Vorschubgeschwindigkeit auf ein Niveau, das der Extruder effektiv verarbeiten kann.
- Eine zu große bzw. zu große Siebmaschenzahl kann zu Widerständen beim Materialtransport und zu Streifenbrüchen führen. Dies sollte durch entsprechendes Verringern der Wirtsgeschwindigkeit oder Erhöhen der Vorschubgeschwindigkeit erfolgen.
- Überprüfen Sie regelmäßig und ersetzen Sie abgenutzte oder beschädigte Schrauben bei Bedarf: Abgenutzte oder beschädigte Schrauben können zu ungleichmäßiger Mischung führen, was zu Streifenbrüchen führen kann.
- Erhöhen Sie die Trommeltemperatur: Durch Erhöhen der Trommeltemperatur wird das Material weicher und das Risiko eines Bandbruchs verringert.
- Die Extrusionstemperatur ist niedrig oder die Schneckenscherung ist zu schwach, und das Material sowie Additive mit niedrigem Schmelzpunkt werden nicht ausreichend plastifiziert, was bei schlecht plastifiziertem Material während der Extrusionsgranulierung auch zum Bruch des Streifens führen kann.
Inkonsistente Partikelgröße
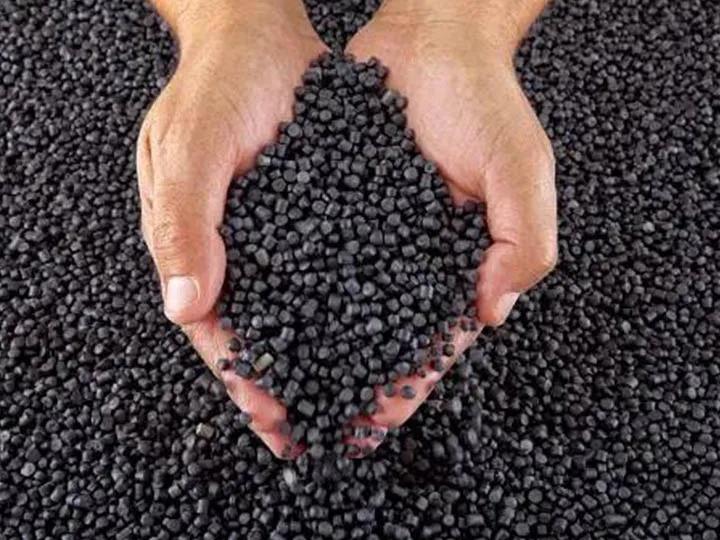
Uneinheitliche Pelletgrößen sind ein weiteres häufiges Problem, das bei der Herstellung von Kunststoffgranulatoren auftritt.
Dieses Problem kann durch verschiedene Faktoren verursacht werden, beispielsweise durch verstopfte Matrizen, verschlissene Schrauben oder beschädigte Schneidmesser. Die folgenden praktischen Lösungen können Ihnen helfen, dieses Problem zu überwinden:
- Auf verstopfte Düsen prüfen: Verstopfte Düsen können zu inkonsistenten Partikelgrößen führen. Wenn es verstopft ist, reinigen Sie es mit einem geeigneten Reinigungswerkzeug.
- Überprüfen Sie die Schrauben: Verschlissene Schrauben können zu unterschiedlichen Pelletgrößen führen. Überprüfen Sie die Schrauben, um sicherzustellen, dass sie nicht abgenutzt oder beschädigt sind. Wenn sie abgenutzt sind, sollten Sie über einen Austausch nachdenken.
- Schneidmesser prüfen: Beschädigte Schneidmesser können zu unterschiedlichen Partikelgrößen führen. Überprüfen Sie das Schneidmesser, um sicherzustellen, dass es nicht beschädigt ist. Wenn sie beschädigt sind, sollten Sie über einen Austausch nachdenken.
- Passen Sie die Schneckengeschwindigkeit an: Die Schneckengeschwindigkeit des Pelletierers beeinflusst die Länge des Austrags, und die Anpassung der Schneckengeschwindigkeit kann dabei helfen, Inkonsistenzen bei der Pelletgröße zu beheben. Sie können die Schneckengeschwindigkeit erhöhen oder verringern, um eine gleichmäßige Pelletgröße zu erhalten.
- Überprüfen Sie die Zufuhrgeschwindigkeit: Eine falsche Zufuhrgeschwindigkeit kann zu unterschiedlichen Pelletgrößen führen. Überprüfen Sie die Vorschubgeschwindigkeit, um sicherzustellen, dass sie nicht zu hoch oder zu niedrig ist. Passen Sie die Zufuhrgeschwindigkeit nach Bedarf an, um gleichmäßige Pelletgrößen zu erhalten.
Zusammenfassend lässt sich sagen, dass die Herstellung von Kunststoffgranulatoren ein komplexer Prozess ist, der je nach Situation gelöst werden muss. Im Produktionsprozess sollten Sie den Gerätestatus überprüfen und die Betriebsparameter rechtzeitig anpassen, um Produktionseffizienz und Pelletqualität sicherzustellen.