Máquina trituradora de garrafas de água, também conhecida como Triturador de garrafas PET, é um tipo de equipamento especializado na trituração de resíduos de garrafas plásticas PET em pedaços, amplamente utilizado na indústria de reciclagem de plásticos. Neste artigo, apresentaremos detalhadamente a estrutura da máquina trituradora de garrafas de água para ajudar os leitores a obter uma compreensão mais profunda de seu princípio de funcionamento e componentes importantes.
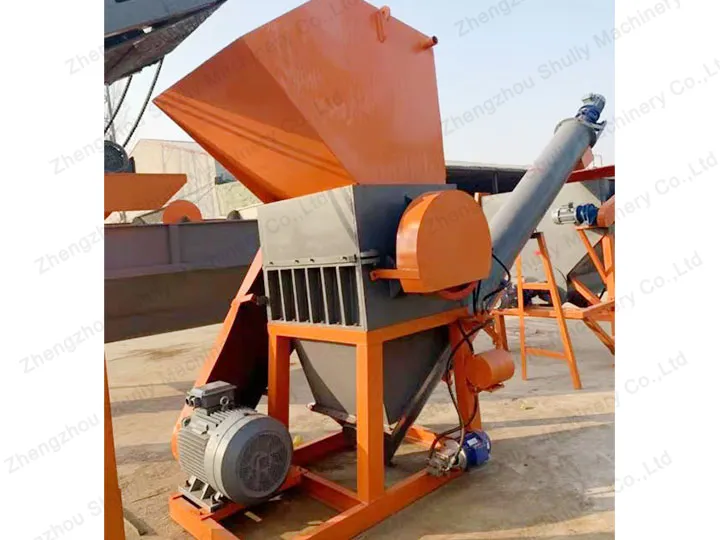
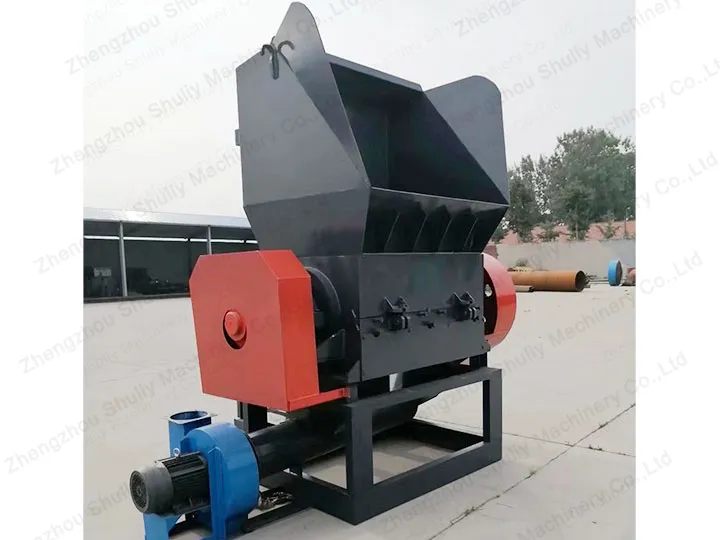
Estrutura geral da máquina trituradora de garrafas de água
A máquina trituradora de garrafas de plástico geralmente consiste nos seguintes componentes principais.
Sistema de alimentação
O sistema de alimentação é a parte inicial da máquina trituradora de garrafas plásticas. Os usuários colocam os resíduos de garrafas plásticas PET na abertura de alimentação e o sistema de alimentação os transporta para a câmara de britagem. Para garantir uma operação segura e eficiente, o sistema de alimentação geralmente é equipado com uma esteira transportadora automática e sensores para interromper ou iniciar o processo de alimentação quando necessário.
Câmara de esmagamento
A câmara de britagem é a parte central da máquina trituradora de garrafas plásticas e é usada para esmagar garrafas PET em pedaços. A câmara de britagem é equipada com lâminas ou martelos de alta resistência, cujo número e layout variam de acordo com as especificações e requisitos da máquina. Quando as garrafas PET passam pela câmara de britagem, as lâminas ou martelos provocam fortes impactos e cortes sobre elas, fazendo com que sejam rapidamente esmagadas em pequenos pedaços.
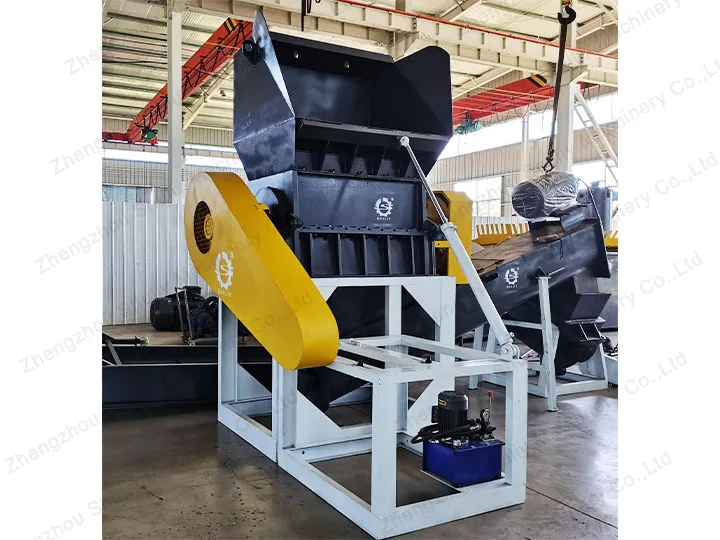
Sistema de descarga
O sistema de descarga é usado para descarregar os chips de PET triturados da câmara de britagem. Normalmente, o sistema de descarga é equipado com uma tela para separar os cavacos do tamanho desejado. Os cavacos maiores não triturados serão realimentados na câmara de britagem até que o tamanho desejado seja alcançado.
Sistema de acionamento elétrico da máquina trituradora de garrafas de água
O sistema de acionamento elétrico da máquina trituradora de garrafas de água fornece energia para acionar a operação de cada componente. Normalmente, um motor elétrico é utilizado como principal fonte de energia, cuja potência e especificação dependem do tamanho e capacidade do britador. O sistema de acionamento elétrico transmite energia para a câmara de britagem e sistema de descarga através de diversas transmissões para garantir sua operação eficiente.
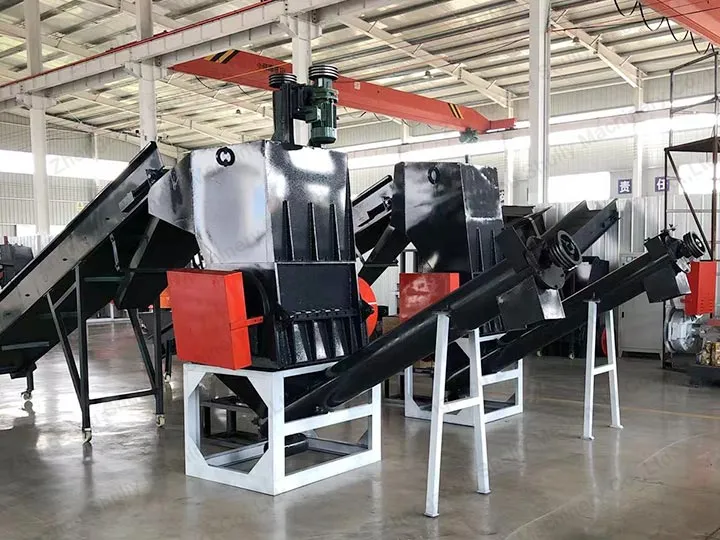
Sistema de controle da máquina de esmagamento de garrafas PET
O sistema de controle é a parte inteligente da britadeira de garrafas PET, responsável por monitorar e controlar todo o processo de britagem. Os britadores de plástico modernos geralmente são equipados com sistemas avançados de controle automático, que podem ser configurados e monitorados por meio de uma tela sensível ao toque ou interface de computador.
Os operadores podem definir o tamanho de chip desejado e a capacidade de produção no painel de controle e monitorar o status de funcionamento do equipamento para garantir uma operação segura e eficiente.
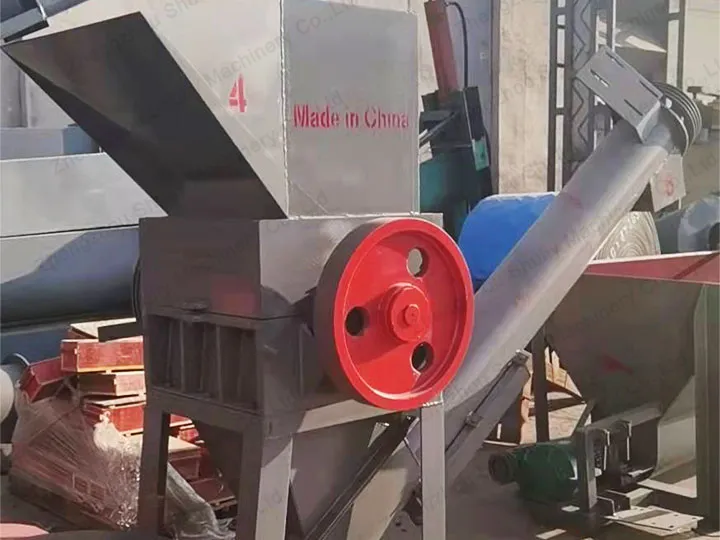
Materiais de construção
A construção do material de uma máquina trituradora de garrafas de água desempenha um papel fundamental em seu desempenho e durabilidade. Para garantir que o equipamento possa suportar impactos e pressões de alta intensidade, os materiais estruturais comuns incluem aço de alta qualidade e ligas especiais. Além disso, as lâminas ou cabeças dos martelos dentro da câmara de britagem são geralmente feitas de materiais de liga resistentes ao desgaste para prolongar a vida útil e melhorar a eficiência.
Instalações de segurança da máquina de esmagamento de garrafas PET
A máquina trituradora de garrafas de água é um equipamento mecânico poderoso, portanto as instalações de segurança são cruciais. Os recursos de segurança comuns incluem proteções, interruptores de segurança e botões de parada de emergência. Estas medidas garantem que o risco de acidentes seja reduzido durante a operação, protegendo ao mesmo tempo o operador. Triturador de plástico Shuliy é seguro e confiável, é sua boa escolha.
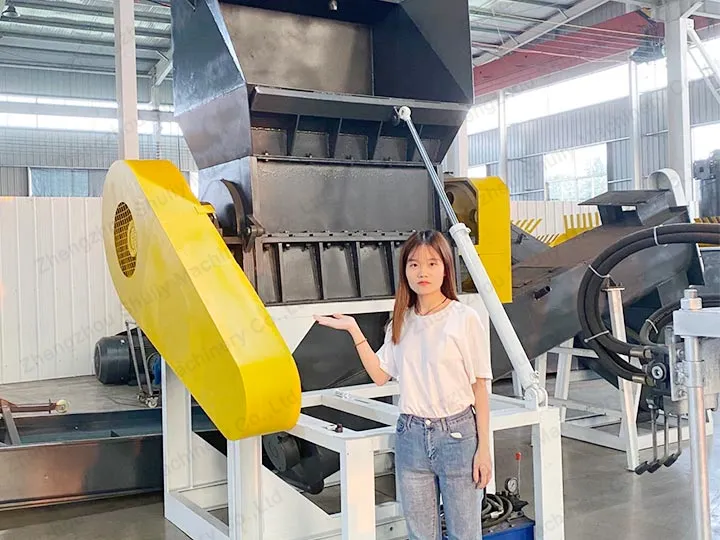
A máquina trituradora de garrafas de água é um equipamento crucial na indústria de reciclagem de plástico e sua estrutura detalhada inclui sistema de alimentação, câmara de britagem, sistema de descarga, sistema de acionamento elétrico, sistema de controle, materiais estruturais e instalações de segurança.
Esses componentes trabalham juntos para permitir que a máquina trituradora de garrafas de água esmague com eficiência garrafas plásticas PET em pedaços. Com o progresso contínuo da ciência e da tecnologia, a máquina trituradora de garrafas plásticas se tornará mais inteligente, eficiente e ecologicamente correta, e dará uma contribuição maior à causa da reciclagem de plástico.