Lini pelet plastik PP PE adalah teknologi utama yang membantu mengurangi limbah sumber daya dan pencemaran lingkungan dengan mengubah limbah film plastik menjadi pelet plastik yang dapat digunakan kembali. Artikel ini akan memperkenalkan 6 langkah utama dalam lini pelet plastik PP PE.
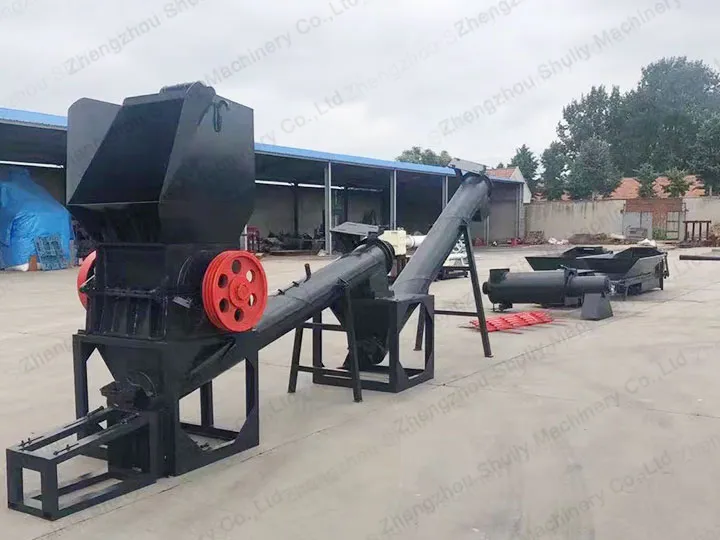
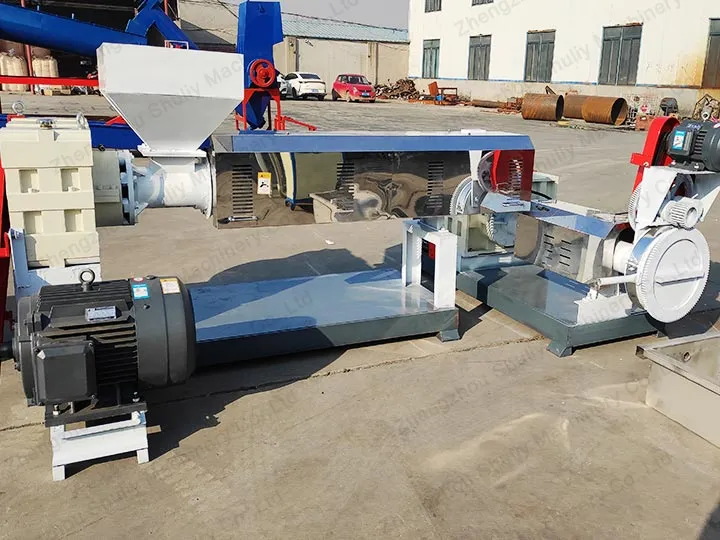
Langkah 1: Menghancurkan garis pelet plastik PP PE
Langkah pertama dalam jalur daur ulang pencucian film plastik adalah memasukkan limbah film plastik yang telah disortir ke dalam penghancur plastik industri. Alat penghancur ini mampu merobek-robek sampah plastik film menjadi potongan-potongan kecil. Pencacahan meningkatkan luas permukaan plastik, sehingga lebih mudah diproses dan meningkatkan efisiensi pemrosesan selanjutnya.
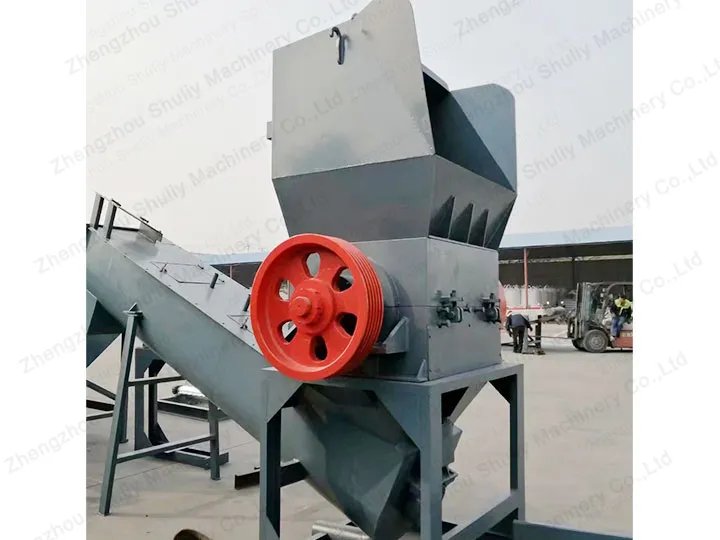
Langkah 2: Mencuci
Setelah diproses di mesin penghancur plastik industri, plastik tersebut mungkin masih memiliki beberapa kontaminan yang menempel di dalamnya, seperti debu, kotoran, dan sisa bahan organik. Oleh karena itu, pada langkah kedua, plastik dimasukkan ke dalamnya mesin cuci film plastik. Mesin cuci memanfaatkan aliran air dan gesekan untuk menghilangkan kotoran permukaan dan memastikan kemurnian plastik untuk proses produksi selanjutnya.
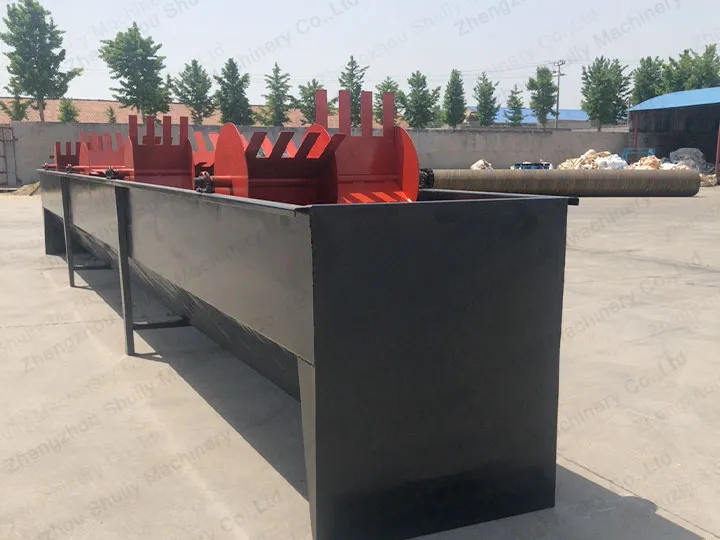
Langkah 3: Dehidrasi
Setelah dicuci, potongan plastik tersebut masih mengandung air. Langkah ketiga adalah memasukkan plastik ke dalamnya mesin pengering plastik. Dengan menggunakan udara panas, pengering menguapkan air untuk membuat plastik mencapai kadar air yang tepat. Pastikan plastik dalam keadaan kering, karena kadar air yang terlalu tinggi dapat mempengaruhi hasil pelet.
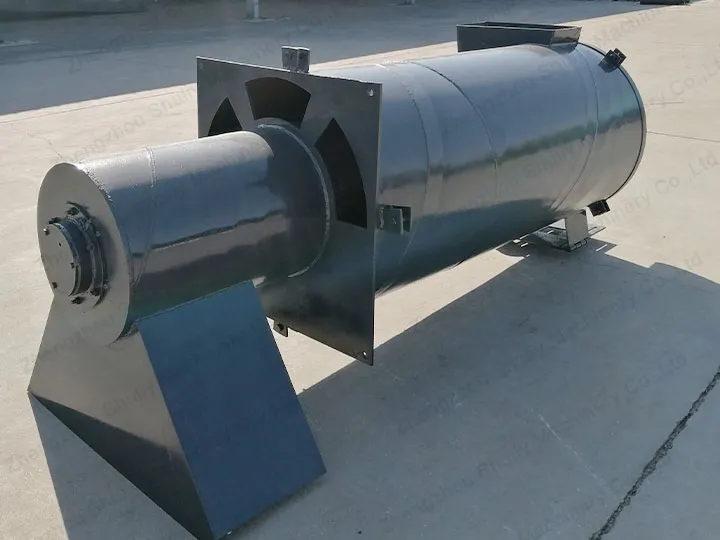
Langkah 4: Pembuatan pelet plastik
Ini adalah langkah inti dalam lini pelet plastik PP PE. Itu ekstruder plastik PP PE memproses plastik melalui suhu dan tekanan tinggi. Plastik dipanaskan dan dicairkan lalu diekstrusi menjadi strip plastik kontinu.
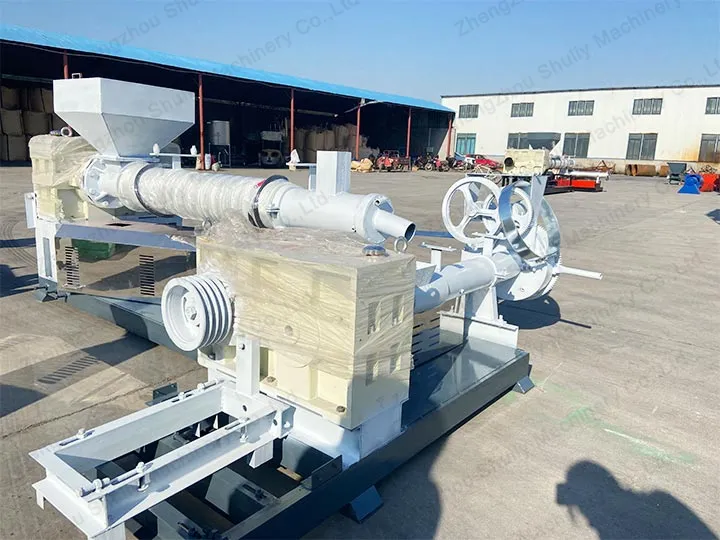
Langkah 5: Pendinginan
Setelah pelet awal, potongan plastik masih berada pada suhu tinggi. Langkah kelima adalah memasukkan potongan plastik ke dalam tangki pendingin. Tangki pendingin diisi dengan air pendingin atau media pendingin lainnya, yang dengan cepat menurunkan suhu strip plastik dan memadatkannya. Proses pendinginan juga membantu meningkatkan kepadatan dan kualitas pelet.
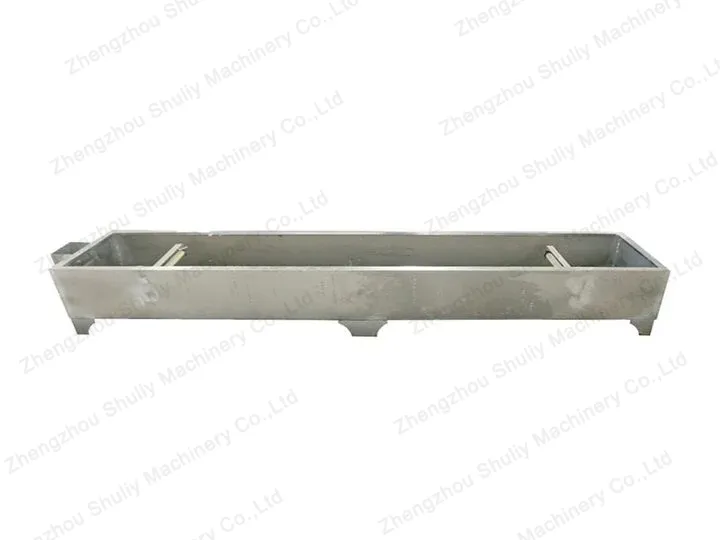
Langkah 6: Pemotongan dan penyimpanan
Terakhir, potongan plastik yang didinginkan dimasukkan ke dalam mesin pemotong pelet plastik. Mesin pemotong pelet plastik mampu memotong strip plastik menjadi ukuran dan bentuk yang diinginkan untuk memastikan memenuhi kebutuhan pelanggan. Pelet plastik yang telah disesuaikan kemudian disimpan dalam silo penyimpanan untuk pengemasan dan pemasaran lebih lanjut.
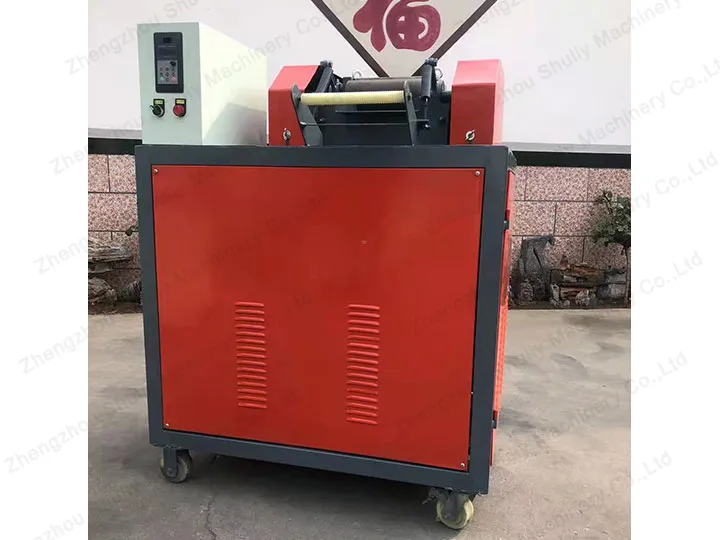
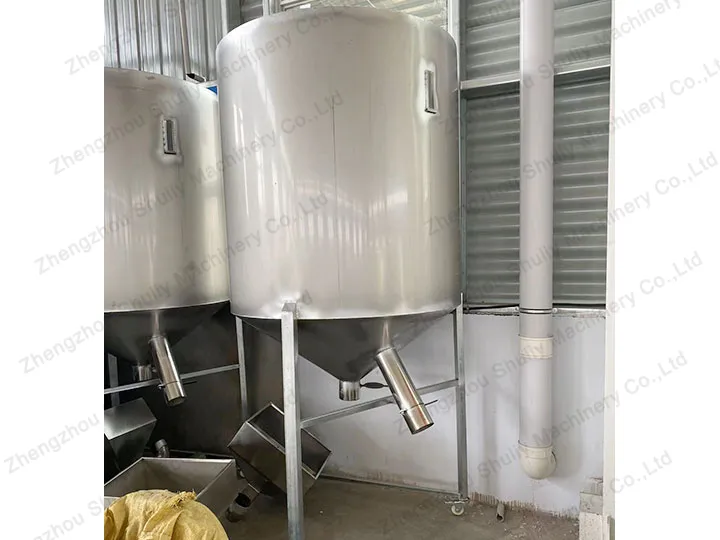
Melalui enam langkah utama lini pelet plastik PP PE, kita dapat mengubah limbah film plastik menjadi pelet plastik yang berguna dan mewujudkan penggunaan kembali sumber daya secara efektif. Seluruh lini pelet plastik PP PE mendukung penyesuaian, jika tertarik, selamat datang untuk menghubungi kami!