Pengekstrusi butiran PP PE mengadopsi desain sekrup khusus dan konfigurasi berbeda, yang cocok untuk memproduksi PP, PE, dan jenis daur ulang plastik lainnya serta granulasi pencampuran warna.
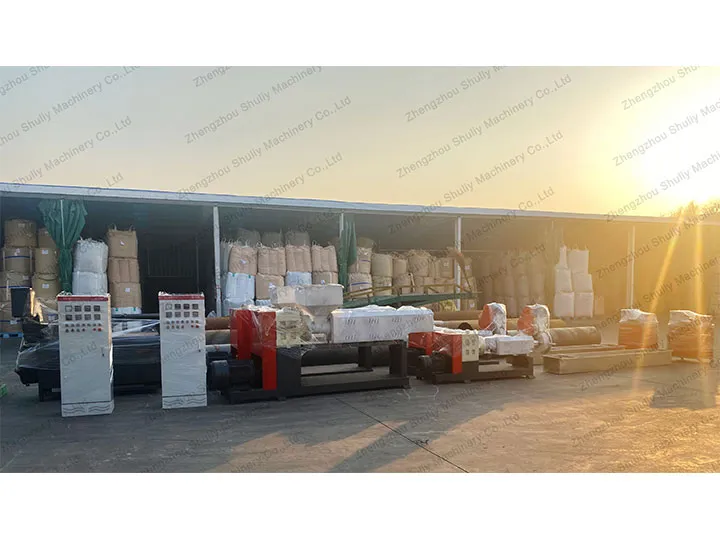
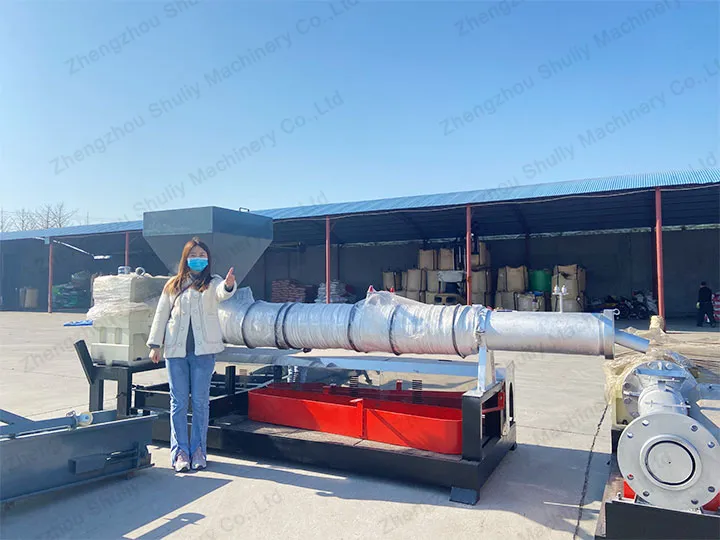
Prinsip kerja ekstruder butiran PP PE
Setelah plastik dimasukkan ke dalam hopper ekstruder butiran PP PE, plastik jatuh dengan mulus dari hopper ke sekrup dan tergigit oleh ulir sekrup. Saat sekrup berputar, sekrup tersebut dipaksa oleh ulir untuk maju ke arah kepala mesin, yang merupakan proses pengangkutan mekanis.
Ketika plastik mengalir menuju kepala mesin dari lubang pengumpanan, kedalaman ulir sekrup secara bertahap berkurang. Juga karena adanya saringan, manifold, dan tahan panas, tekanan yang sangat tinggi terbentuk dalam proses plastisisasi, yang menekan material dengan sangat kuat, meningkatkan perpindahan panasnya, dan membantu plastik meleleh dengan sangat cepat. Pada saat yang sama, tekanan meningkat secara bertahap sehingga asli adanya gas di antara material dari lubang pembuangan.
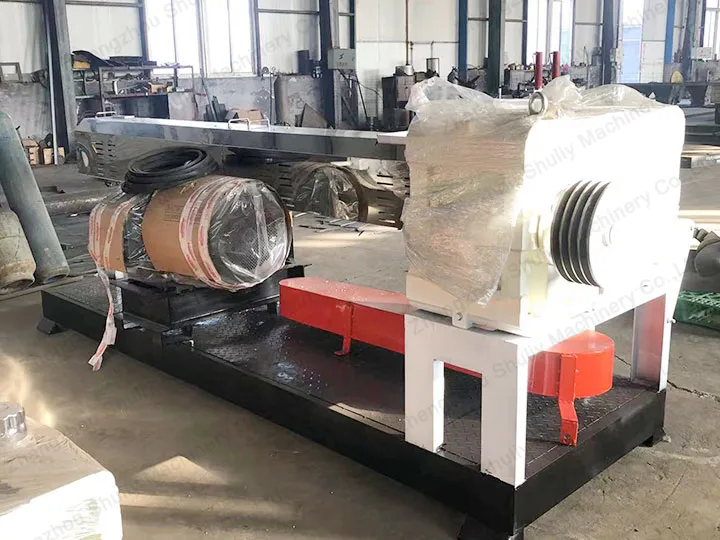
Pada saat yang sama ketika tekanan meningkat, plastik dipanaskan secara eksternal di satu sisi. Di sisi lain, plastik itu sendiri dalam proses kompresi, geser, dan gerakan pengadukan, akibat gesekan internal juga menghasilkan banyak panas.
Di bawah pengaruh gabungan kekuatan eksternal dan internal, suhu plastik secara bertahap naik dan mencapai titik leleh dan mulai meleleh. Dengan pengangkutan material, pemanasan yang terus berlanjut, jumlah material cair secara bertahap meningkat, dan penurunan yang sesuai terjadi pada pencatatan material non-cair.
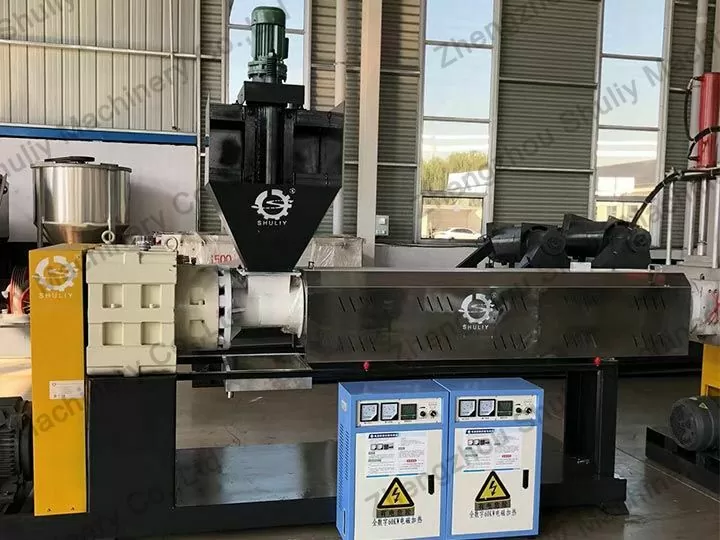
Pada akhir bagian kompresi, semua material diubah menjadi keadaan aliran kental. Namun kemudian suhu tiap titik belum seragam setelah bagian homogenisasi efek homogenisasi lebih seragam. Setelah sekrup melelehkan material secara kuantitatif, tekanan tetap dan suhu tetap berada di kepala.
Kepala cetakan adalah bagian cetakan yang melaluinya material memperoleh geometri dan ukuran penampang. Seiring dengan mengecilnya diameter material, aliran dipercepat menuju ujung pelepasan dan akhirnya melewati lubang cetakan ke dalam tangki air pendingin dalam keadaan terkelupas untuk didinginkan dan dibentuk.
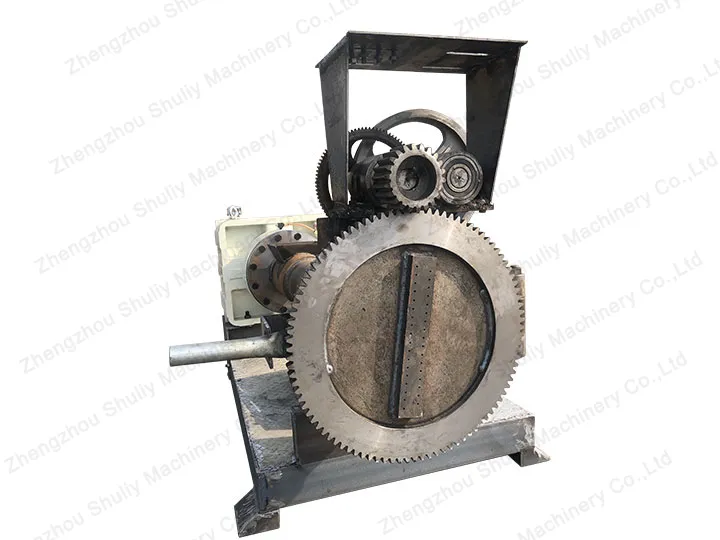
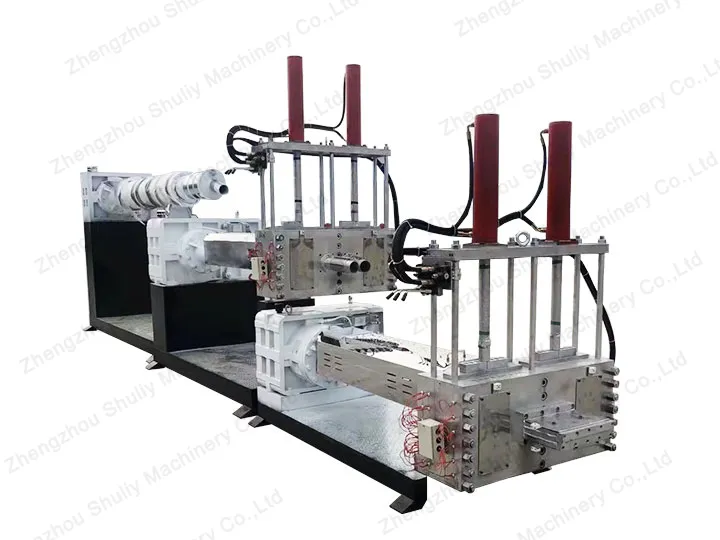
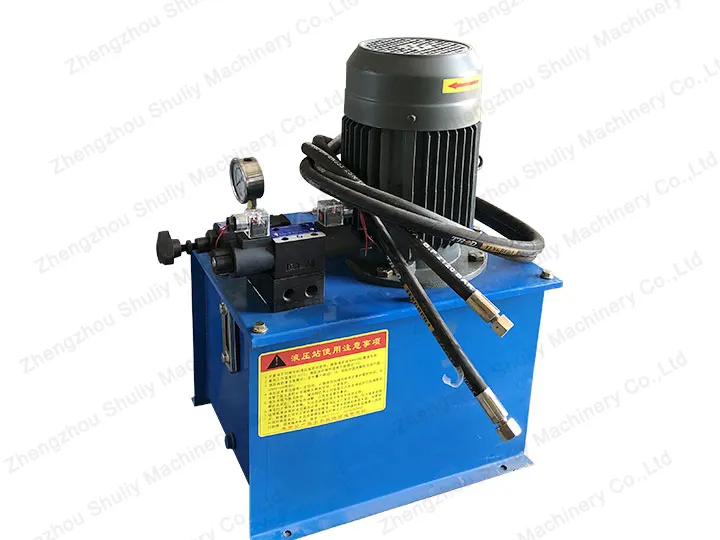
Akhirnya, ia terjepit oleh roller traksi mesin pemotong plastik dan secara serempak dimasukkan ke dalam ruang pisau mesin pemotong plastik, di mana pemotong berputar berkecepatan tinggi memotong strip plastik menjadi partikel-partikel kecil, sehingga menyelesaikan seluruh proses granulasi.
Karakteristik ekstruder butiran PP PE
- Tingkat teknologi otomasi ekstruder butiran PP PE tinggi. Mulai dari penghancuran bahan mentah, pembersihan, dan pengumpanan hingga pembuatan butiran, semuanya dilakukan secara otomatis. Biaya tenaga kerja rendah, efisiensi produksi tinggi, dan keuntungan tinggi, sangat mengurangi biaya produksi.
- Pengekstrusi butiran PP PE memanfaatkan sepenuhnya sistem pemanas gesekan tanpa gangguan bertekanan tinggi, produksi pemanasan otomatis, menghindari pemanasan terus menerus, penghematan daya, dan penghematan energi.
- Mesin pelet daur ulang plastik mengadopsi sistem distribusi daya otomatis penuh untuk memastikan pengoperasian motor yang aman dan normal.
- Barel sekrup mesin pelet daur ulang plastik terbuat dari baja struktural karbon impor berkekuatan tinggi dan berkualitas tinggi, tahan lama.
- Penampilan mesin granulator plastik cantik dan murah hati. Itu bisa dicat sesuai dengan kebutuhan pelanggan.
- Gearbox reduksi ekstruder butiran PP PE mengadopsi desain torsi tinggi untuk mencapai kinerja pengoperasian tanpa suara dan mulus. Sekrup dan laras diperlakukan dengan perlakuan pengerasan khusus, yang memiliki karakteristik ketahanan aus, kinerja pencampuran yang baik, dan output tinggi.
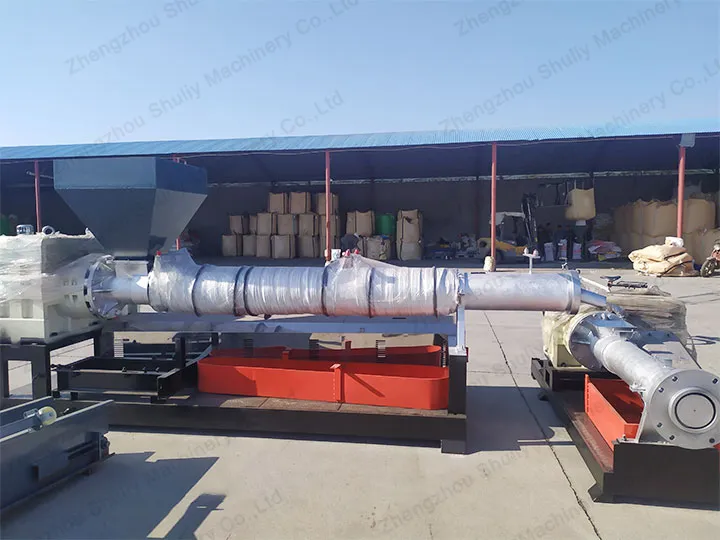
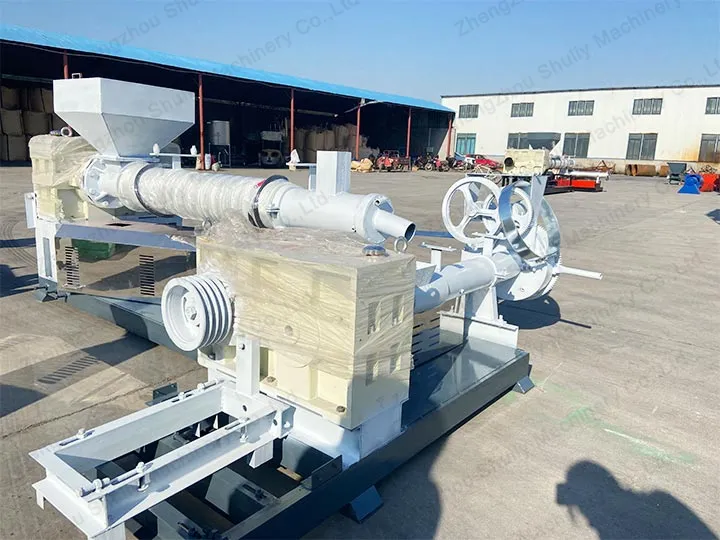