Plastic extruder pellets machine is an indispensable and important piece of equipment in the plastic recycling process, which can process waste plastic into recycled plastic pellets.
Reasonable operation and maintenance are crucial before the plastic extruder pellets machine stops. This article will introduce the work that should be done before the shutdown of plastic extruder pellets machine to ensure productivity and equipment life.
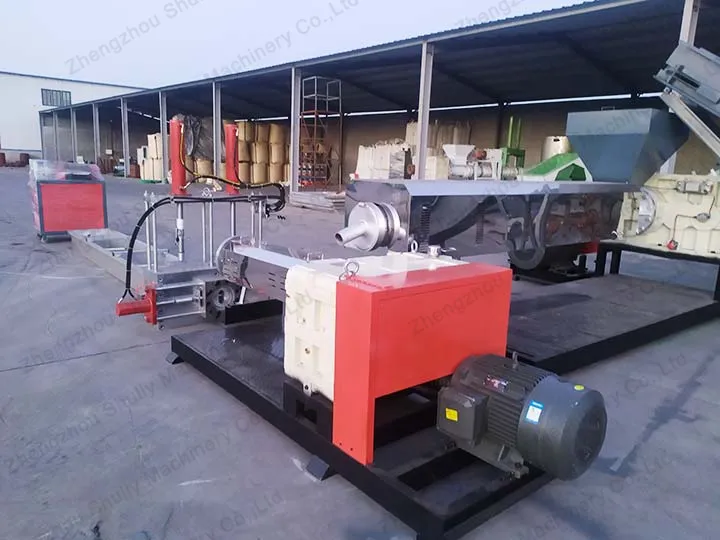
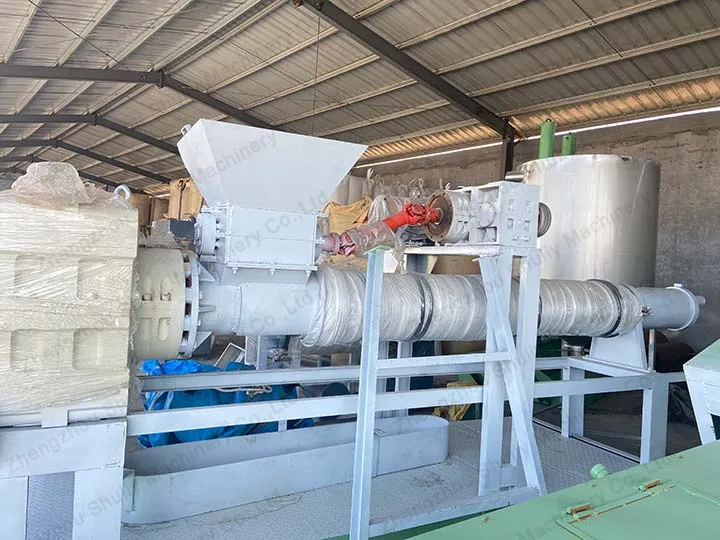
Cleaning the plastic extruder pellets machine
Before stopping the machine, all parts of the recycled plastic pelletizing machine must be thoroughly cleaned. First, stop the feed and wait until the plastic is completely emptied. Then, turn off all switches, dismantle the die head and screen, and use special tools to remove any residue from them. At the same time, wipe the surface of the machine with the cleaner to make sure it is dust-free and pollution-free, ready for the next start-up.
Check the cooling system
The cooling system of the recycled plastic pelletizing machine is vital for temperature control during production. Before stopping the machine, check the operation status of the cooling system to ensure that the cooling water flow is smooth and the cooling effect is good. If abnormalities are found, clean or replace the cooling water pipe in time to avoid equipment failure or product quality problems caused by high temperature.
Maintenance screw and mold
The screw and mold of plastic extruder pellets machine are the core parts directly involved in plastic processing. Before stopping the machine, the screw and mold must be inspected and maintained. Check the wear degree of the screw, if there is serious wear, it needs to be replaced in time. At the same time, clean the residue on the surface of the mold to maintain the finish and precision of the mold to ensure the quality of the recycled plastic pellets.
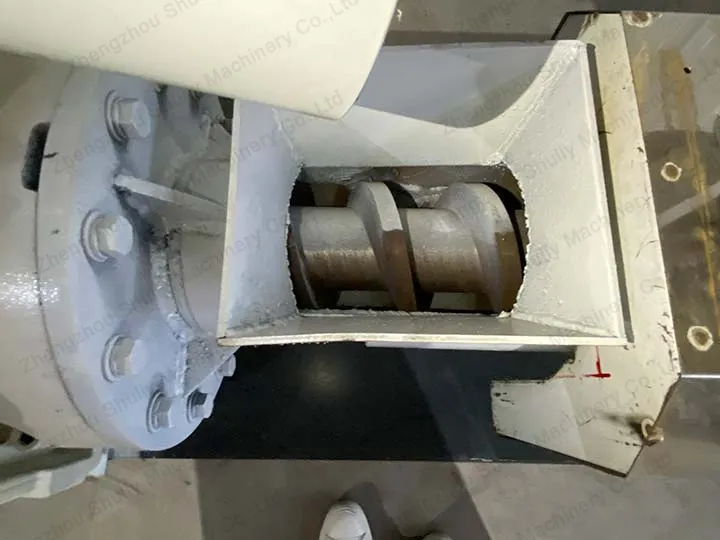
Checking the screen and die head
The screen and die head are very critical parts of the plastic extruder pellets machine, and their condition directly affects the quality of the pellets. Before stopping the machine, the screen and die head should be carefully inspected to make sure there are no residual plastic particles or debris on their surfaces. If any blockage or damage is found, they should be replaced or repaired in time so as not to affect the processing effect of the next production.
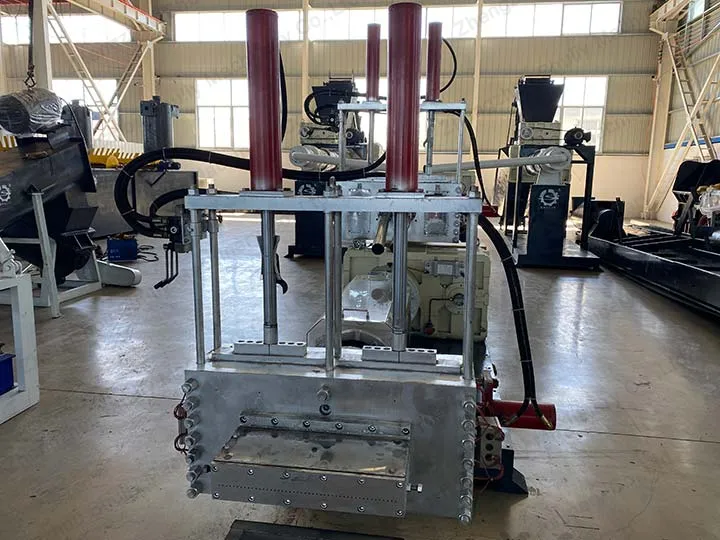
Empty the barrel and storage hopper
Before stopping the machine, empty the plastic pellets in the barrel and hopper to avoid mixing different kinds of plastics in the next production process, which will lead to unstable product quality. At the same time, check whether there is any accumulation of impurities inside the barrel and storage hopper of plastic extruder pellets machine, if so, clean them up in time to ensure the cleanliness of the production environment.

Turn off the power and gas source
Before shutting down, make sure to turn off the power supply and gas source of the plastic extruder pellets machine to avoid unnecessary energy waste and equipment damage. At the same time, turn off the relevant water and oil sources to ensure that the equipment is in a safe and energy-saving state in the shutdown state.
Pelletizer equipment is important equipment for plastic recycling, in order to ensure the normal operation of the pelletizer equipment and extend its service life, the necessary work before the shutdown is particularly important.
Before the shutdown, do a good job of cleaning, inspection, and maintenance, not only can extend the service life of the equipment but also to ensure that the next start can be efficient and stable production.
Through the reasonable operation of the above aspects, we can better protect the plastic extruder pellets machine and extend the service life of the recycled plastic pelletizing machine.