Les extrudeuses de déchets plastiques, en tant qu'équipement important dans le traitement des plastiques recyclés, et leurs techniques de fonctionnement sont essentielles à l'amélioration de la qualité des granulés recyclés. Cet article explique comment utiliser un pelletiseur plastique pour améliorer la qualité des pellets recyclés et ainsi mieux répondre aux enjeux environnementaux.
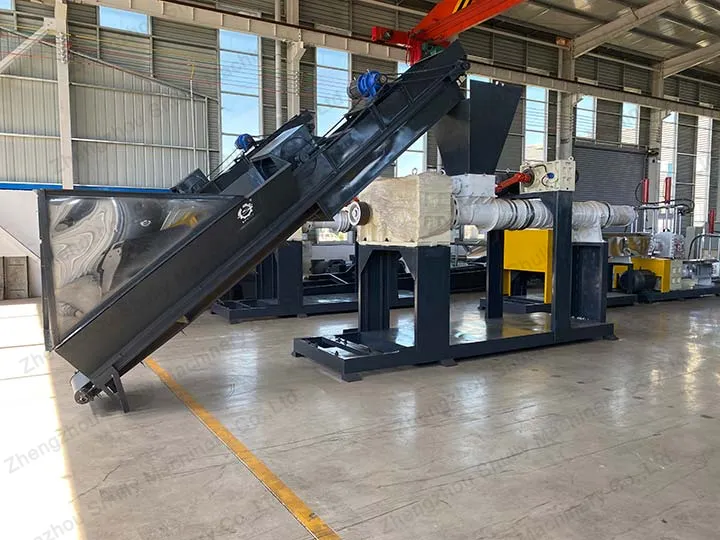
Assurer la propreté des matières premières
Avant de pelletiser avec une extrudeuse de déchets plastiques, il est important de garantir la propreté de la matière première. Les déchets plastiques sont souvent mélangés à des impuretés telles que des résidus alimentaires et de la poussière. Ces impuretés peuvent affecter la qualité des pellets recyclés et le fonctionnement de la machine. Par conséquent, avant de nourrir, il est important d’effectuer un nettoyage et un criblage approfondis pour garantir la pureté de la matière première.
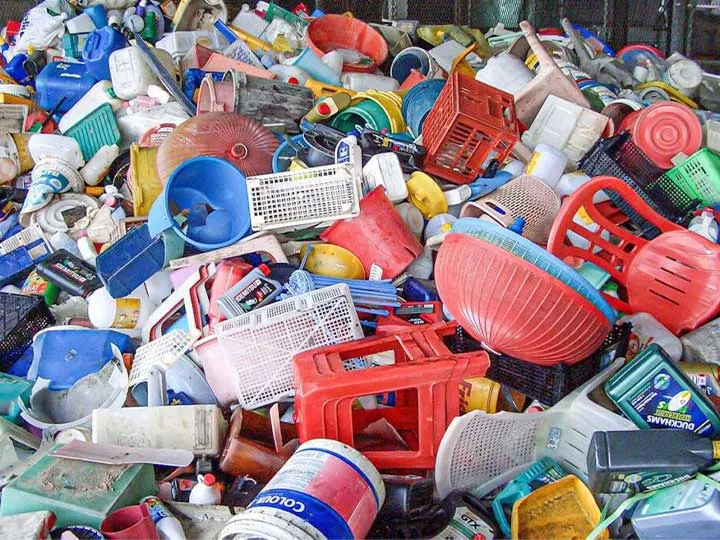
Contrôler la température et la pression du granulateur
La température et la pression de l'extrudeuse de déchets plastiques sont des facteurs importants affectant la qualité des granulés recyclés. Une température et une pression appropriées garantissent que le plastique est entièrement fondu et uniformément réparti, ce qui donne des granulés recyclés de haute qualité. Des températures et pressions excessivement élevées ou basses peuvent entraîner une détérioration de la qualité des pellets. Par conséquent, la température et la pression de extrudeuse de granulés de plastique doivent être étroitement surveillés et réglementés pendant le fonctionnement.
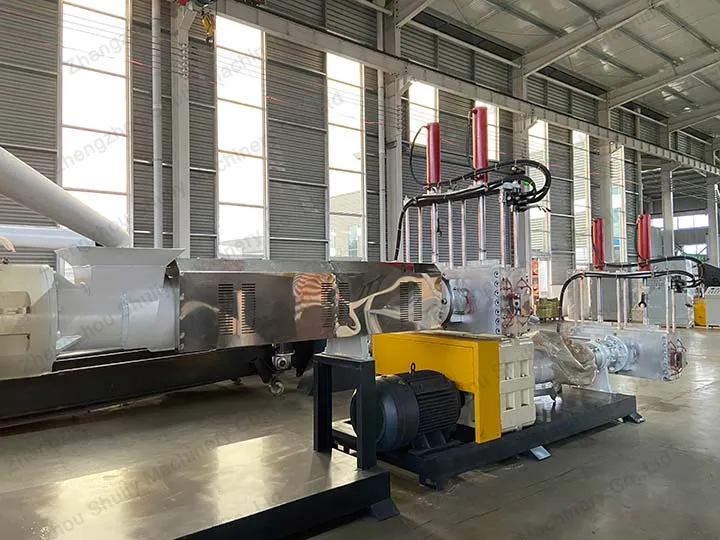
Choisir la bonne extrudeuse de déchets plastiques
Différents types de déchets plastiques peuvent nécessiter différents types de granulateurs de plastique pour être traités. Choisir le bon type d'extrudeuse de granulés de plastique et d'équipement adapté aux caractéristiques de la matière première est la clé pour améliorer la qualité des granulés recyclés. Par exemple, pour certains déchets plastiques spéciaux, un granulateur de plastique spécialement conçu peut être nécessaire pour garantir des résultats de traitement et une qualité de granulés optimaux.
Entretien et maintenance réguliers
Un entretien et un entretien réguliers sont essentiels pour assurer le bon fonctionnement de la machine d'extrudeuse de déchets plastiques et pour maintenir la qualité des granulés. Des mesures telles que le nettoyage de l'intérieur de la machine, le remplacement des pièces usées et la lubrification de la machine peuvent prolonger la durée de vie de la machine tout en garantissant une qualité constante des granulés.