Mit dem Pelletierextruder für Kunststoffe werden Kunststoffabfälle erhitzt, komprimiert und geschmolzen und dann durch den Extruderkopf geleitet, um sie zu Kunststoffpellets zu formen. Allerdings kann es im Produktionsprozess manchmal zu einem Bruch des Kunststoffstreifens kommen, der die Produktionseffizienz und die Produktqualität beeinträchtigt. In diesem Artikel gehen wir auf die Ursachen gebrochener Streifen in PE-Granuliermaschinen ein und stellen entsprechende Gegenmaßnahmen vor.
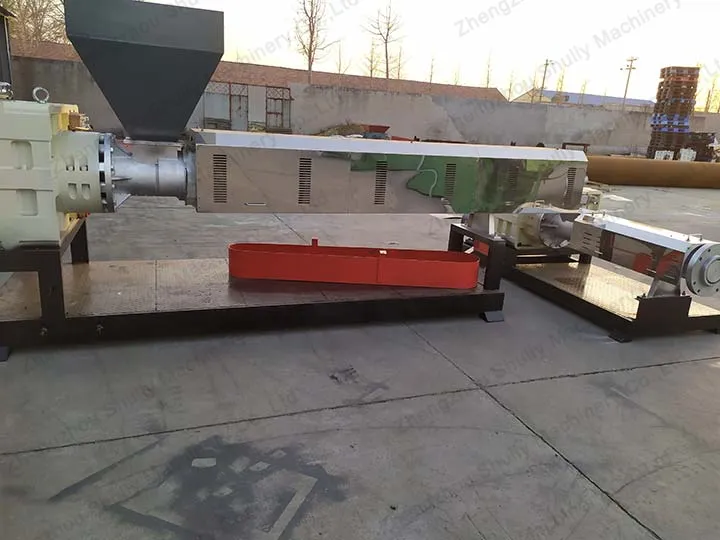
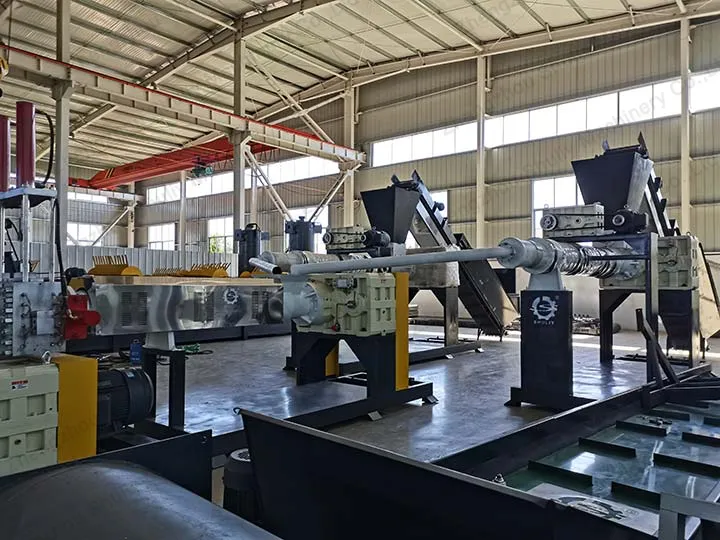
Ursache für ein Problem mit gebrochenen Kunststoff-Granulierextrudern
- Unsachgemäße Temperaturkontrolle: Kunststoff-Granulierextruder erfordern eine präzise Steuerung der Heiztemperatur, um sicherzustellen, dass der Kunststoff vollständig geschmolzen und reibungslos extrudiert werden kann. Wenn die Temperatur nicht richtig eingestellt ist, schmilzt der Kunststoff nicht ausreichend, was zu gebrochenen Stäben führt.
- Probleme mit dem Extruderkopf: Der Extruderkopf ist eine der kritischsten Komponenten in einem Kunststoff-Granulierextruder. Wenn der Kopf nicht richtig konstruiert oder beschädigt ist, kann es leicht zum Bruch des Kunststoffstreifens kommen.
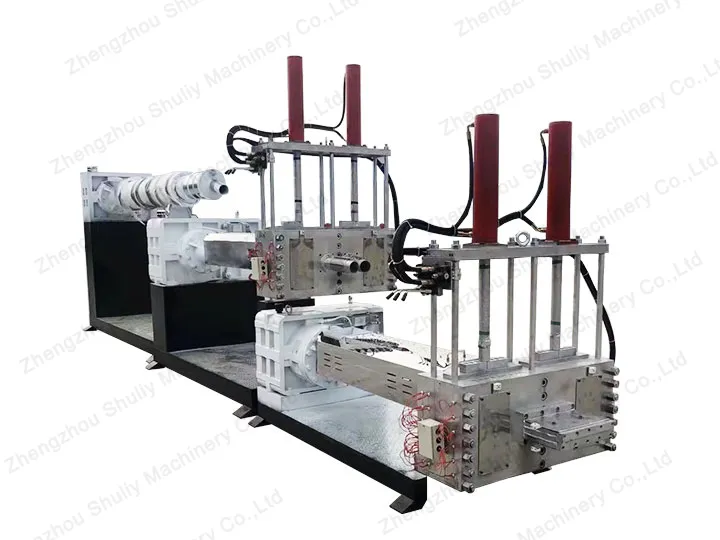
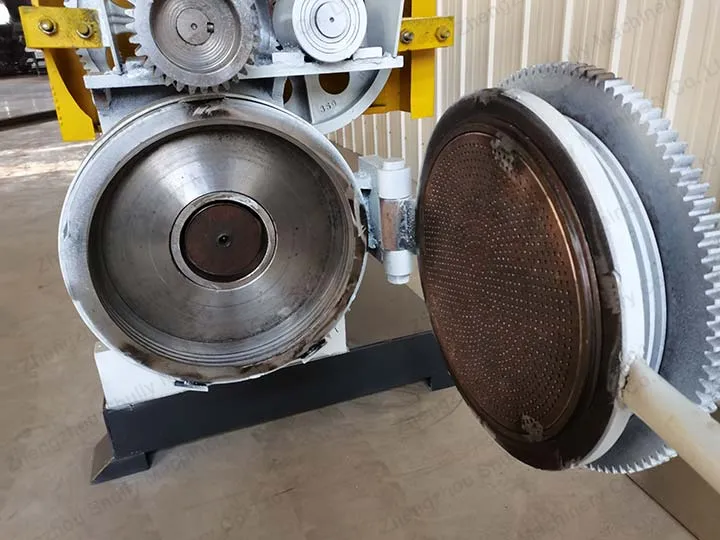
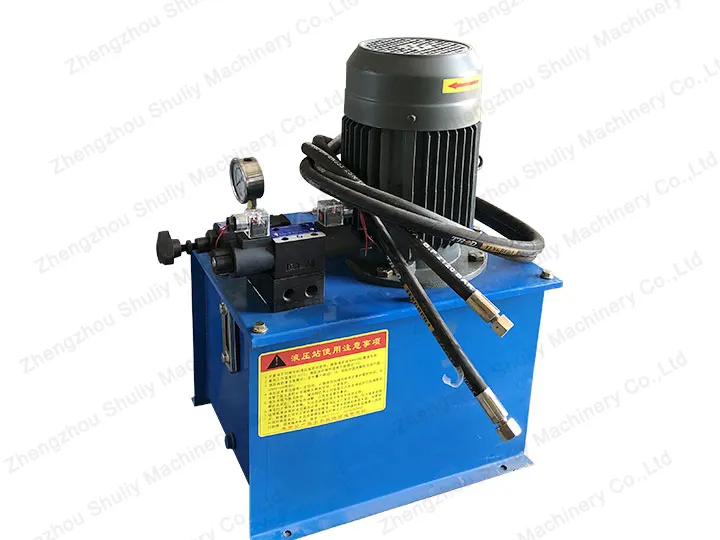
- Der Extrusionsdruck ist zu hoch oder zu niedrig: Die Extrusionsschnecke im Inneren des Kunststoffgranulierungsextruders übt einen bestimmten Druck aus, um den Kunststoff nach vorne zu drücken und durch den Extrusionsauslass Pellets zu bilden. Der Extrusionsdruck des Kunststoff-Granulierextruders muss richtig eingestellt werden. Zu groß oder zu klein kann zur Instabilität der Kunststoffpartikel und dann zum Phänomen gebrochener Streifen führen.
- Abnormale Kühlwassertemperatur: Nach der Extrusion muss der Kunststoff schnell mit Kühlwasser abgekühlt werden, damit er zu Pellets erstarrt. Wenn die Kühlwassertemperatur abnormal ist oder die Wasserversorgung instabil ist, führt dies zu ungleichmäßigen oder zerbrochenen Kunststoffpellets.
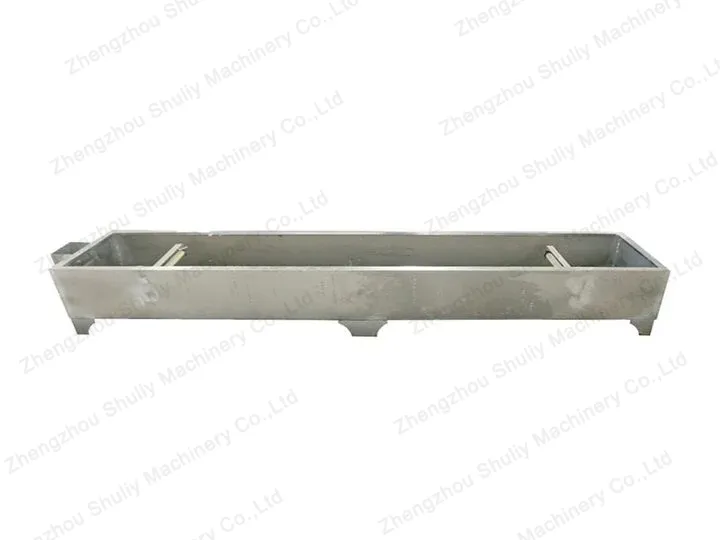
- Abgenutzte Schnecken: Längerer Betrieb und Umgebungen mit hohen Temperaturen können zu Verschleiß an den Schnecken der PE-Granuliermaschine führen und deren Extrusionseffizienz verringern. Eine verschlissene Schraube ist möglicherweise nicht in der Lage, den Kunststoff effizient zu drücken, was dazu führt, dass der Kunststoff in Streifen zerbricht.
Lösungen für gebrochene Streifen in Kunststoff-Granulierextrudern
- Kontrollieren Sie die Temperatur genau: Überprüfen Sie regelmäßig das Heizsystem der Maschine zur Herstellung von Kunststoffpellets, stellen Sie die Genauigkeit des Temperatursensors sicher, stellen Sie die Temperatur auf den entsprechenden Bereich ein und vermeiden Sie, dass zu hohe oder zu niedrige Temperaturen zu Streifenbrüchen führen.
- Überprüfen Sie den Extruderkopf: Überprüfen Sie regelmäßig den Verschleiß des Extruderkopfes, tauschen Sie ihn rechtzeitig aus, wenn Sie eine Anomalie feststellen, und stellen Sie sicher, dass der Kopf gut konstruiert ist, um zu verhindern, dass Kunststoffgranulate beim Extrusionsprozess blockiert werden.
- Passen Sie den Extrusionsdruck entsprechend an: Passen Sie den Extrusionsdruck des Extruders entsprechend den Eigenschaften des Kunststoffs und der Produktionssituation an, um eine stabile Extrusion von Kunststoffgranulat zu gewährleisten.
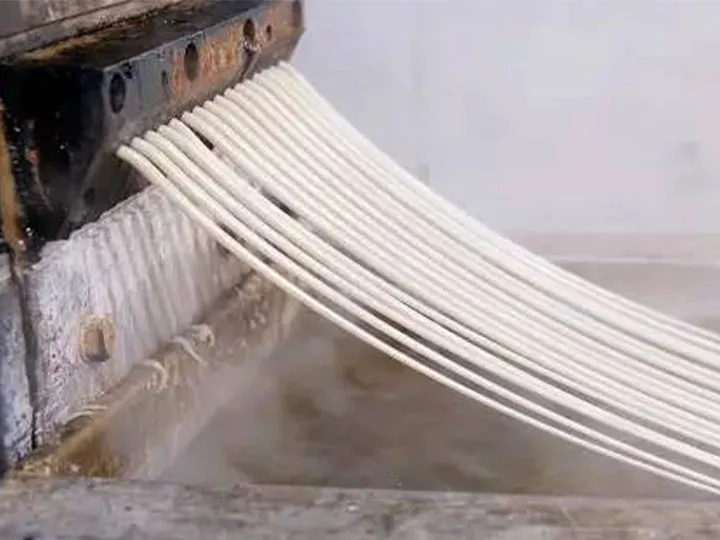
- Optimieren Sie das Kühlsystem: Stellen Sie sicher, dass die Kühlwassertemperatur stabil ist und der Wasserdurchfluss ausreichend ist. Passen Sie das Kühlsystem entsprechend an, um sicherzustellen, dass das Kunststoffgranulat schnell abgekühlt und ausgehärtet wird, um das Problem gebrochener Stäbe zu vermeiden.
- Überprüfen und ersetzen Sie die Schnecke regelmäßig: Überprüfen Sie regelmäßig den Verschleißgrad der Schnecke und ersetzen Sie die Schnecke bei starkem Verschleiß rechtzeitig, um die Extrusionseffizienz und Produktqualität sicherzustellen. Darüber hinaus ist die Auswahl qualitativ hochwertiger Schrauben auch eine wirksame Maßnahme, um Schraubenverschleiß vorzubeugen.
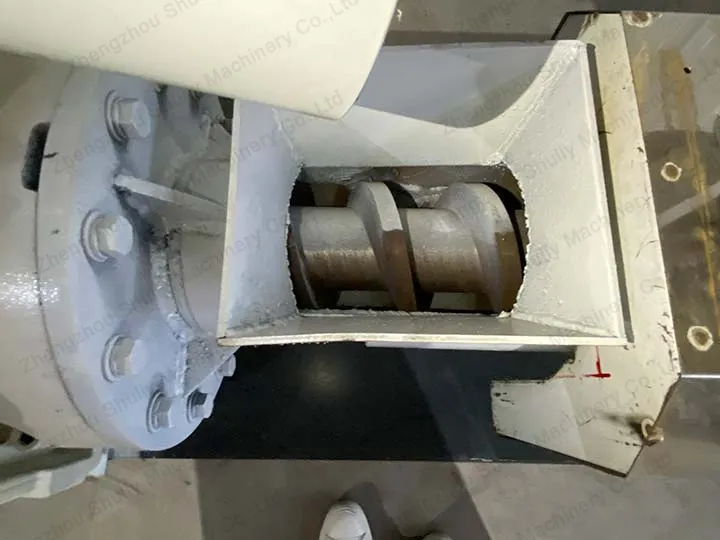
Shuliy Kunststoffgranulator zu verkaufen
Shuliy ist ein professioneller Hersteller von Kunststoff-Granulierextruder. Die Maschinen zur Herstellung von Kunststoffpellets werden mit fortschrittlicher Technologie und hochwertigen Materialien hergestellt, um das Problem des Bandbruchs zu vermeiden. Die hergestellten Kunststoffpellets sind von ausgezeichneter Qualität und entsprechen den Bedürfnissen der Kunden.
Bei Interesse können Sie sich gerne an uns wenden, um detailliertere Informationen zum Preis, den Parametern und anderen Details der Kunststoff-Pelletiermaschine zu erhalten.
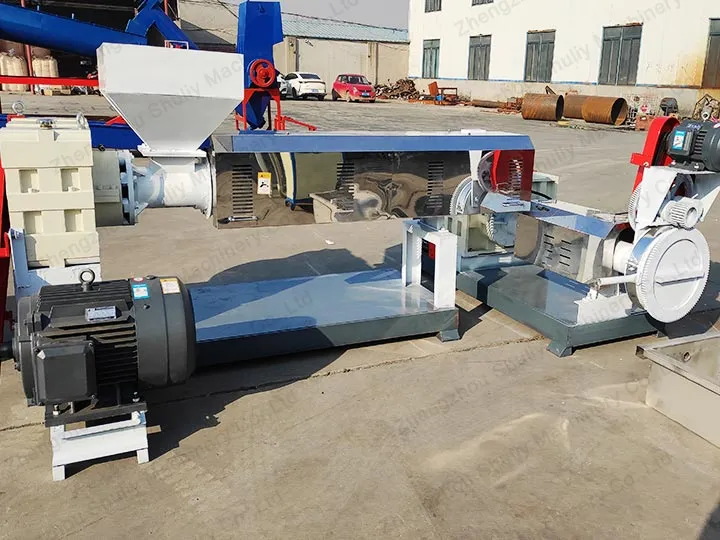
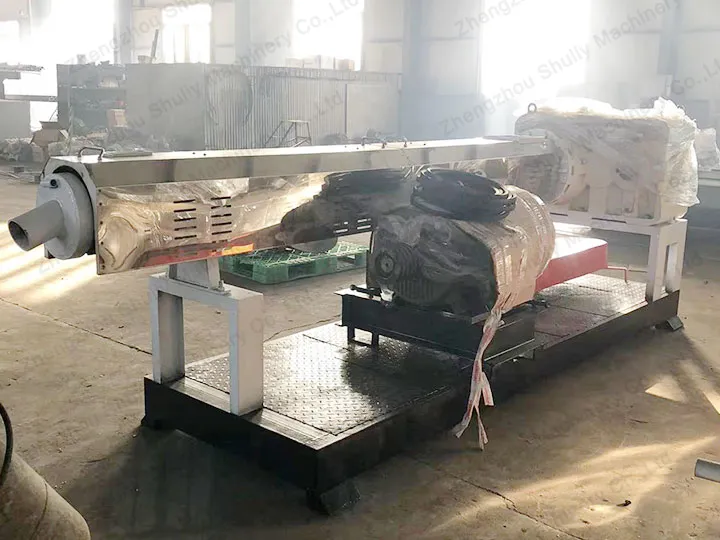