Das Kunststoffrecycling durch Granulatoren ist ein integraler Bestandteil des Kunststoffrecyclingprozesses und wandelt Kunststoffabfälle in wiederverwendbare Kunststoffpellets um. Eine ordnungsgemäße Schmierung ist jedoch unerlässlich, um den effizienten Betrieb und die langfristige Nutzung von Kunststoffgranulatoren sicherzustellen. In diesem Artikel stellen wir vor, wie die Schmierarbeiten richtig durchgeführt werden Granulator Kunststoffrecycling um ihren reibungslosen Betrieb zu gewährleisten und ihre Lebensdauer zu verlängern.
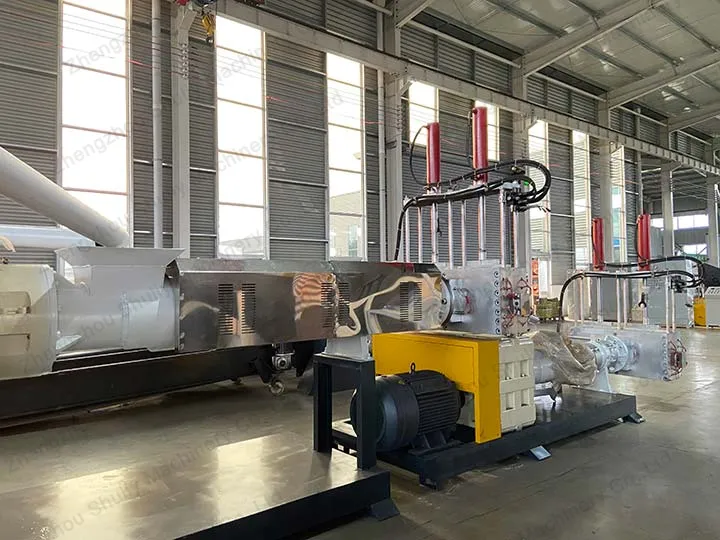
Warum muss das Kunststoffrecycling von Granulatoren geschmiert werden?
Der Kunststoff einer Extrudermaschine muss bei der Verarbeitung große Mengen an Kunststoffrohmaterial verarbeiten, was zu hohen Temperaturen und hoher Reibung führen kann. Erfolgt die Schmierung nicht rechtzeitig, können Maschinenteile durch Reibung verschleißen, die Produktivität beeinträchtigen und sogar die Anlage beschädigen. Daher ist die Schmierung ein wichtiger Schritt, um den normalen Betrieb des Kunststoffextruders sicherzustellen.
Auswahl des richtigen Schmiermittels
Die Auswahl des richtigen Schmiermittels für das Kunststoffrecycling Ihres Granulators ist ein entscheidender Schritt. Zu den gängigen Schmierstoffen gehören Schmierstoffe, Fette und Schmierstoff-Fett-Gemische. Stellen Sie sicher, dass das von Ihnen ausgewählte Schmiermittel eine gute Viskosität und Haftung aufweist, damit es bei hohen Geschwindigkeiten nicht leicht ausgespült wird.
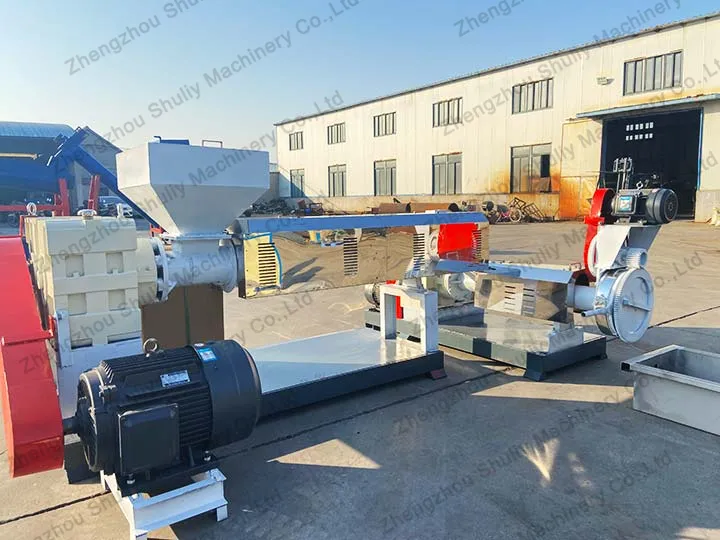
Identifizierung von Schmierstellen
Bevor mit dem Schmiervorgang begonnen wird, müssen die Schmierstellen am Kunststoffrecycling-Granulator eindeutig identifiziert werden. Zu diesen Schmierstellen gehören in der Regel Lager, Zahnräder, Ketten und andere Komponenten. Stellen Sie sicher, dass jede Schmierstelle rechtzeitig geschmiert wird, um Verschleiß und Ausfälle zu verhindern.
Regelmäßige Schmierung
Das Kunststoffrecycling von Granulatoren erfordert eine regelmäßige Schmierung, um sicherzustellen, dass sie immer in gutem Betriebszustand sind. Es wird empfohlen, einen Schmierplan zu erstellen, dessen Schmierintervalle sich nach dem Produktionsvolumen und der Nutzungshäufigkeit richten. Eine tägliche Schmierung ist normalerweise eine gute Wahl, bei hoher Belastung oder hoher Betriebsfrequenz kann jedoch eine häufigere Schmierung erforderlich sein.
Achten Sie auf die Menge der Schmierung
Nicht zu viel oder zu wenig schmieren. Zu viel Schmierung kann zum Verschütten und Verunreinigen von Schmiermittel führen, während zu wenig Schmierung zu erhöhter Reibung und beschleunigtem Verschleiß der Teile führen kann. Bestimmen Sie die richtige Schmiermittelmenge anhand der Empfehlungen des Herstellers und der tatsächlichen Bedingungen.
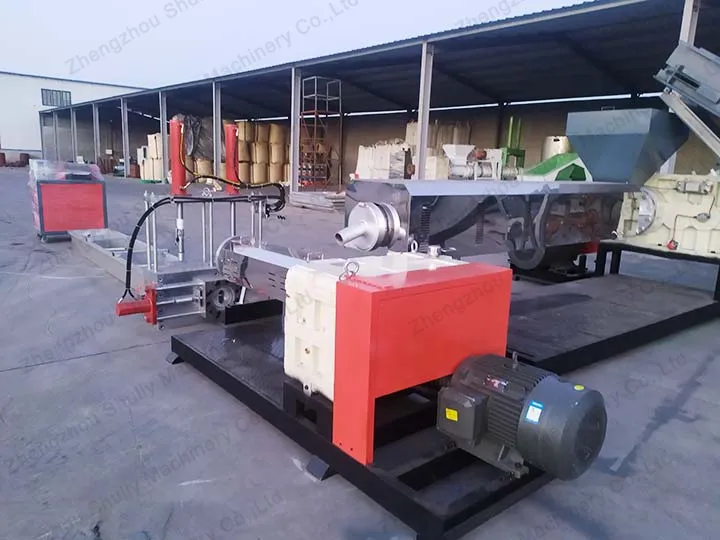
Verwenden Sie die richtigen Werkzeuge
Bei der Durchführung von Schmierarbeiten ist es wichtig, die richtigen Werkzeuge zu verwenden. Das Schmiermittel sollte mit einem speziellen Schmiergerät oder einer Fettpresse aufgetragen werden, um sicherzustellen, dass das Schmiermittel präzise an die Schmierstelle abgegeben werden kann. Dies verhindert die Verschwendung von Schmiermittel und verbessert die Schmierwirkung.
Regelmäßige Inspektion und Wartung
Überprüfen Sie regelmäßig die Schmierung des Extrudermaschine aus Kunststoff um sicherzustellen, dass das Schmiersystem normal funktioniert. Tauschen Sie Schmiermittel und Schmiermittel rechtzeitig aus, um zu verhindern, dass Verunreinigungen in das Schmiersystem gelangen. Wenn außerdem ungewöhnliche Geräusche oder Vibrationen festgestellt werden, stoppen Sie das Kunststoffrecycling des Granulators sofort zur Inspektion und ergreifen Sie entsprechende Wartungsmaßnahmen.
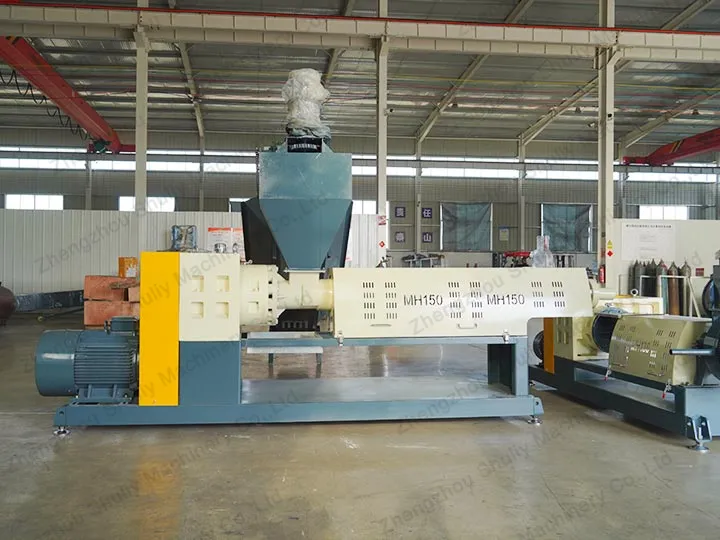